车底威胁是所有军用地面车辆的一个由来已久的问题。据估计,在越南战争期间,73% 的车辆损失是由于杀伤人员地雷和反坦克地雷造成的。虽然机动性和保护系统的发展已帮助作战人员避免此类威胁,但车辆底部库存的快速补充仍然至关重要。
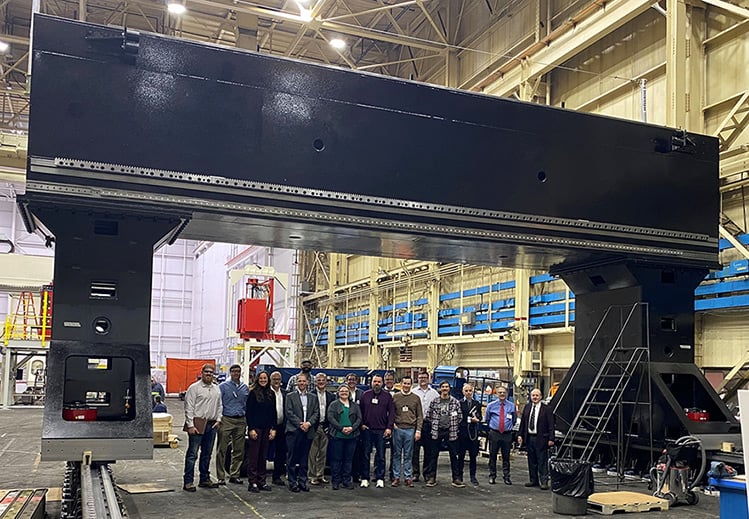
以前的陆军 ManTech 船体底板计划侧重于诸如强化船体结构的锻造和成型以及高能埋弧焊等技术,以最大限度地减少焊缝孔隙率。重点是在制造过程中需要较少焊接接头的较厚车辆底部车体的制造方法,dir从而提高船体抵抗车身底部攻击的耐用性。他们能够展示成功的制造和材料质量,但限制了几何设计的自由度和制造灵活性。真正通用的技术能够探索新的设计概念、快速实施和适应多种车辆平台的灵活性。锻造、成型和焊接未能很好地满足车辆项目需求。
增材制造 (AM) 技术为材料加工和柔性制造提供了新机遇,为生产新车体概念提供了令人信服的途径。
增材制造方法通常可以描述为一种自由形式的制造系统,它通过数字控制材料处理单元以设计的形状一次一层地构建零件来创建零件。增材制造工艺不需要额外的工具,例如模具。与增材制造相比制造、减材制造从大量材料(块、板、棒等)开始,并有选择地去除不需要的材料,直到保留设计零件的形状。
用于创建大型金属部件的增材制造系统功能——例如整车外壳——仍处于起步阶段。一些金属 AM 功能已被证明具有尺寸限制,在一个平面或轴上很大。用于金属 AM 技术的商用现成系统通常具有大约 1 x 1 x 1 m 的最大构建体积,并且可以实现许多应用机会。大面积增材制造 (AM) 系统 (>1 m3) 近年来得到了证明,最突出的是用于加工聚合物材料,因此主要限于模具应用。将可用的技术和机器功能扩展到更大的平台,以实现访问广泛的大规模应用程序的通用功能,尤其是在元l, 是必需的。
项目概述——创建大型金属增材制造机器

ASTRO America, ALMII, and US Army DEVCOM -GVSC 在一项赞助计划中合作,为美国陆军的岩岛兵工厂生产大型金属 AM 系统,以制造陆军地面车辆中常见的大型金属部件。该计划的愿景是将历来在各个行业中得到验证的大型机床与增材制造技术相结合,以缩短生产周期。由此产生的能力将使金属增材制造达到尚未广泛展示或可用的规模,不仅适用于地面车辆系统,而且适用于所有大规模应用。能够打印如此大的金属部件将为应用开辟新的机会,并扩大 additi 的用途五个制造流程。
当前项目将制造和交付两台独立的机器。第一台机器将能够打印和加工尺寸最大为 1 x 1 x 1 m 的零件,并且作为关键的里程碑演示器,该构建体积的零件(图 1a 和 2a)。该机器将用于执行所需的工艺开发、打印策略和打印路径规划,以构建达到其尺寸限制的零件,以及将在第二台更大的机器上构建的零件。第二台较大的机器将能够在其 10 x 6.5 x 4 m(长 x 宽 x 高)的构建体积内打印和加工零件(图 1b 和 2b)。图 1b 显示了将在该程序结束时生成的第二个全尺寸系统的三维渲染图。迄今为止,该系统将是已公开发布的最大的金属增材制造系统。
团队概况——不同的专业知识,共同的目标
为该项目选择的团队机器的设计、构建和开发是一项由系统集成商、工业硬件和软件开发人员以及金属 AM 工艺开发人员组成的协作工作。这些专业知识的结合使该团队能够创造出前所未有的能力。

参与此项目的团队成员包括:
Ingersoll Machine Tools,罗克福德,伊利诺伊州:机床制造商,在为航空航天工业的复合材料加工(即“超大型”部件)构建机器人系统方面拥有丰富的经验。他们使用现成的(即西门子)组件和软件,但构建龙门系统并进行系统集成。他们最近改造了用于打印大型 23' 长(7 m)复合材料工具的产品。
Siemens Industry, Inc., Elk Grove Village, Ill.: The Siemen被选中参与该计划的团队专注于其中的多轴、基于 CNC 的应用程序和过程模拟。他们的目的是让大型 AM 系统利用商用硬件和软件产品,并开始构建系统独有的工艺规划程序。
MELD Manufacturing Corp.,Christiansburg,弗吉尼亚州:开发商在 MELD 工艺(也称为添加剂搅拌摩擦沉积)中,MELD Manufacturing Corp. 正在生产和交付沉积系统,这些系统将使这些大型金属 AM 机器的添加剂组件成为可能。他们的专利加工技术在固态工艺中利用锻造原料材料,该工艺依靠严重的塑性变形在沉积点沉积材料。
创建大规模金属增材制造意味着什么
该项目考虑了所有商用金属添加剂技术。但是,有一小部分非常适合d 并且能够在项目规模要求范围内进行缩放以生产组件。为大型机器选择的配置是一台移动龙门机器,金属打印和加工工具直接安装在机器的一个轴(Z 方向)上。这种配置有利于处理大型(重型)金属部件,并允许灵活地操纵制造方法,包括集成多种制造技术,在这种情况下,增加了加工能力。
打印大型部件需要大量材料,处理原料是另一个主要考虑因素。许多流行的金属增材制造技术都使用金属粉末作为原料。虽然送粉(或吹粉)定向能量沉积系统已经证明能够扩展到一些更大的尺寸,但基于粉末床的技术还没有。在开发这些技术时大规模系统的技术不断发展,与处理和加工金属粉末相关的固有挑战将继续存在,并将随着系统规模扩大到更大尺寸而被放大。
大型零件的挑战和规模化
在增材制造中,材料从一层到下一层的连接是工艺和技术的一个关键方面。材料的连接是增材制造工艺和减材制造工艺之间的根本区别之一。在许多金属增材制造工艺中,材料的连接是一种基于熔化的工艺,需要将原料材料和来自前一层的材料加热到超过熔化温度,以便通过熔化和沉积金属随后的快速凝固实现连接。通过仔细控制过程中传递到材料上的能量,可以准确(使用激光或电子束)或快速(使用金属丝或粉末进料)打印材料和构建零件。
但是,随着尺寸的增加,基于熔体的连接过程可能会带来挑战。在制造大型零件时,材料反复熔化和凝固导致的残余应力问题可能会给打印零件时保持几何公差带来挑战。随着零件尺寸的增加,随着零件变得越来越大,累积效应会加剧残余应力问题。
低温增材制造方法被认为有助于减少应力和应力累积过程。 MELD Manufacturing 独特的基于固态摩擦搅拌的添加剂工艺被选为最有希望满足我们大型系统的尺寸和材料需求的工艺。该技术由一个中空的旋转台肩组成,材料通过该台肩输送并沉积到基板上。从工具头到原料的旋转和压力导致塑性变形和沉积的材料流动将其置于基板或先前沉积的层上。

与其他基于沉积的 AM 技术一样,沉积头在机器的构建区域周围移动,通常以 1 毫米厚和 38 毫米宽的量级沉积单道材料。由于 MELD 过程是一种固态过程,因此材料保持在其熔化温度以下,避免了材料的重复熔化和凝固,并最大限度地减少了极端的热梯度和过大的残余应力。 MELD 的固态工艺能够在沉积材料的同时将温度保持在材料熔化温度的 60-90%。此外,固态工艺避免了应力累积导致的材料开裂,并可以减少(或防止)可以观察到的空隙(即孔隙率)的形成与基于熔体的增材制造工艺相结合。由于 MELD 制造的部件是完全致密打印的,因此它们不需要二次加工来去除任何体积缺陷,例如空隙或孔隙率。此外,据报道,MELD 工艺可产生精细的等轴晶粒结构,从而在“印刷”状态下提供更好的材料性能,这与基于熔体的添加剂技术或铸造部件相反,后者表现出更大的定向凝固晶粒和更低的材料在“印刷/铸造”状态下的性能。
MELD 技术的较低材料加工温度突出了一些优于更传统的制造方法和其他大型增材制造系统的优势。例如,由于材料是在低于材料熔化温度的温度下打印的,因此系统本身不需要专门的腔室(即真空腔室、惰性气体环境、先进的空气处理)。机器ne 在制造业典型的开放式仓库式环境中操作和打印零件。不受机器室和相关操作要求的限制或限制还允许过程的灵活性和可重构性,并且还需要更少的时间来进行给定组件所需的生产准备。 MELD 过程与材料无关,这意味着我们可以研究超出当前技术水平的未来材料。尚未开发的下一代材料可以提供更好的性能。
结论

实现金属增材制造,规模足够大为了维持陆军地面车辆,该计划中正在开发的系统必须考虑和解决许多挑战和方法。目标是创建一个系统,可以快速制造大型金属结构,适用于需要金属材料特性的广泛应用。在考虑了金属 AM 工艺具有扩大到更大尺寸的潜力的挑战和局限性之后,确定固态工艺是实现预期尺寸规模的最佳选择。作为该项目机器开发的一部分,将对制造材料样本进行测试和分析,以优化系统的加工条件并表征最终使用特性。最终,目标将是生产一个灵活的制造系统,扩展制造能力以满足许多需求,包括车辆规模零件的维持、准备以及设计和性能的进步。
注意:作者承认感谢位于密歇根州底特律的美国轻质材料制造创新研究所 (ALMII) 对项目的项目管理贡献。
分发 A. 批准公开发布; d分配无限制。 OPSEC#6283