
大幅面增材制造 (LFAM) 机器制造商继续遵循物理定律。
一家公司刚刚售出其有史以来最大的 3D 打印机,能够制造近 20' ( 6.1 m)长。另一个制造了可以 45° 角打印的 LFAM 机器。还有一个拥有一台专门用于制造复合模具的新机器,可以同时打印和铸造工具。
与此同时,随着计算能力继续接管当今机床的更多操作,大型-格式 3D 打印机也不例外。
无需手动校准
位于马萨诸塞州威尔明顿的 BigRep America Inc. 可能是最新的 LFAM 机器制造商h 控制其中一台机器运行的大脑,从而产生了 Pro.2。有了新型号,打印床、挤出机和双挤出机构的手动校准已成为过去。
“如果从外面看,它看起来完全一样,但我们真正专注于关于易用性,”位于柏林的母公司 BigRep GmbH 的产品营销主管 Marco Mattia Cristofori 说。 “我们在 MXT 控制系统上做了大量工作,因此计算机更加智能。主要重点是让用户只专注于切片和准备 G 代码。”
MXT 系统的更新是 BigRep 新 Jumpstart 的一部分,这是一种“混合软件-硬件解决方案,让您跳过麻烦,直接开始打印,”该公司网站称。 Jumpstart 还有两个组件:Switchplate,一个可移动且灵活的打印床,可在磁铁的帮助下卡入到位;和 Lockstage,一个简单和安全的电子援助xtruder 安装,挤出机也卡入到位。
新模型由 BigRep 的 Precision Motions Portal 提供支持,这是一个定制的龙门架,由 Bosch Rexroth CNC 组件提供动力,包括带有集成编码器的伺服电机。
p>“门户更轻便,可以真正提高准确性和速度,”Cristofori 说。
Metso Outotec 是一家为矿物加工和金属精炼行业提供设备和解决方案的全球供应商,它使用通过首先将木块粘合在一起来制作用于金属铸造的模具和芯盒。然后,将用 CNC 数控系统对所得木坯进行铣削。
然而,2021 年 2 月,该公司在巴西的铸造厂安装了 BigRep Pro,这在很大程度上取代了对重型木块的需求。在其 Pro 上打印 70 个零件后,负责铸造厂 3D 打印的 Patricia Moraes 指出,美卓将模型成本降低了 70%,加快了生产速度,使聚合物模型的处理变得容易更简单,因为它们比木头更轻,并释放了以前为木头保留的存储空间。
两个挤压机,一个部件
BigRep 最近还改进了其旗舰型号 One,以生产One.4。 One.4 是完全可配置的,可以使用单挤出机、双挤出机和双挤出机。双模式允许用户在第二台挤出机中使用水溶性支撑材料进行打印。或者,他们可以在挤出机中使用两种具有不同机械性能的材料,以用于更复杂的应用。
相同的材料可用于印刷品及其支撑物,它们会立即折断。美洲销售总监蒂姆·鲁夫纳 (Tim Ruffner) 说,但要“彻底”改善表面光洁度,用户应该看看 BigRep 的水溶性支撑材料,它可以完全洗掉。总部位于德国的垃圾收集车制造商 Zoeller 将其在 2019 年购买的一台车辆升级为双挤压机,以提高产量。
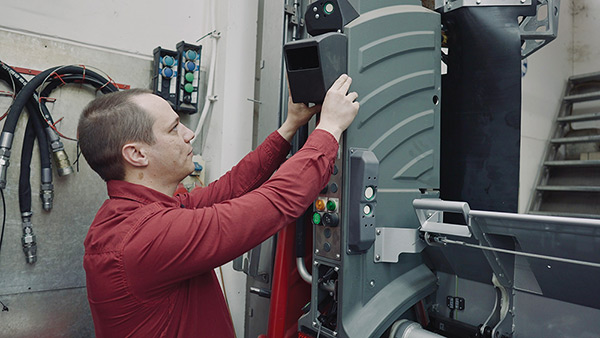
使用 3D 打印加快原型迭代有助于Zoeller 需要不断适应其在许多不同国家使用的车辆的特定国家安全和保护法规。由于下一代车辆使用机械升降机而不是人工垃圾处理机,因此车辆还必须能够举起不同的车辆...的复杂性,精度和材料特性。
3D 打印给公司带来了多么大的不同:原型迭代现在需要几天,而不是几周;客户可以快速检查更改的零件,同时他们的想法在他们的脑海中是新鲜的;打印出的原型很容易安装在车辆上,因此可以在现实条件下进行测试。
45° 的柔性打印
2020 年,Thermwood Corp. 和 General Atomics Aeronautical Systems Inc. 对制造 CNC 装饰工具的两种增材制造方法进行了正面比较。
这家航空航天公司使用手工铺层工艺制造碳纤维层压板装饰工具,该工具用于在加工时固定另一个模具或工具。 Thermwood 使用 20% 碳纤维填充的 ABS 颗粒在其 LSAM(大规模增材制造)1020 上 3D 打印了一个 1,190 磅(539.77 千克)的部件。

“在我们打印并加工它之后,他们根据节省成本等因素对其进行了自己的测试。他们回来说我们节省了印第安纳州戴尔市 Thermwood 营销副总裁 Duane Marrett 说:“与他们使用的传统方法相比,成本约为 50,000 美元。打印需要 16 个小时,修整需要 32 个小时。通常需要六到八周的时间从头到尾他们以前的做法,而使用 LSAM 只用了不到两周的时间。”
打印和修边都在 1020 内,这要归功于机器的两个龙门架中的第二个, 这个用于五轴 CNC 路由器。“他们可以在 sa我的时间——一个在打印,另一个在修剪,”Marrett 说。该机器的双重用途特性并不是 1020 多功能性的唯一展示。
Thermwood 为该机器配备了三种打印模式——水平、垂直和倾斜,“这是我们最新的事情,”马雷特说。角度层打印使用特殊的工作台和打印头的独特设置以 45° 角分配材料。 “这提供了很大的灵活性,”Marrett 说。
对于海洋工业,Thermwood 使用 Techmer Electrafil ABS LT1 3DP 为 White River Marine Group 3D 打印了船体图案。虽然该模式不是像通用原子公司那样的面对面演示,但制造该零件的传统方法包括必须使用木头或泡沫层粘合空白,然后将大部分材料加工掉,这一过程可能需要几个月的时间。
“这是一个新的设计,Thermwood 执行副总裁 Jason Susnjara 在回应关于显示船体打印的 YouTube 视频的评论时说。
整个打印、组装和装饰过程需要不到 10 个工作日即可完成,并使用了大约 15,000 美元的材料。一旦 Thermwood 将船体的部分 3D 打印成近净尺寸,那里的操作员就会使用属于 LSAM 一部分的 CNC 加工中心对端部进行加工以使其变平。然后,他们使用环氧树脂将这些部分粘合在一起。
“就像为任何东西制造工具一样,如果你从一大块材料开始,你最终会加工掉大部分材料,”Susnjara 说. “我们提供的 CNC 加工中心就是这样做的。 3D 打印允许我们打印比最终尺寸稍大的物体,需要更少的材料去除。 3D 打印也比机加工更快。一般来说,我们发现机加工的时间比普通机加工的时间长 3 倍左右。打印周期,取决于几何形状和光洁度。”
决定打印速度的主要是打印聚合物的冷却速率。因为 LSAM 的珠子是一个相对较大的 0.5 英寸(12.7 毫米),打印机在室温环境下工作。打印的珠子必须冷却到足以支撑下一层,但仍然必须足够热才能与其完全融合. 这意味着有一个特定的温度范围,对于每种聚合物来说都是不同的。这个时间量是印刷层最快的时间,无论其尺寸如何。
预测未来
位于芝加哥的西亚基公司的焊接和 3D 打印技术均由电子束提供动力,该公司在 2022 年初获得了有史以来最大的订单。该订单包括定制的 EBAM 300 系列增材制造系统——世界上最大的电子光束定向能量沉积金属 3D 打印机——用于土耳其航空航天工业 (TAI) 在土耳其安卡拉。 TAI 将使用西亚基 EBAM 机器打印钛航空结构。
TAI 和西亚基之间的合同还包括在一系列旨在优化客户对 EBAM 机器及其技术的使用的项目上进行合作。
“总的来说,我们使用高价值材料,如钛、铌、铬镍铁合金、钽——很多材料都非常适合航空航天和国防,当然这些材料被认为非常坚固,适用于非常恶劣的环境崎岖;西亚基母公司 Phillips Service Industries Inc. 的公共关系总监 Jay Hollingsworth 说。
除了进行 3D 打印外,EBAM 300 还可以具备进行大规模应用的电子束 (EB) 焊接的能力。这意味着 TAI 将具有结合电子束焊接和 3D 打印功能的优势,适用于需要这两种技术的应用s.
“AM 系统可以快速切换以执行焊接功能,”Hollingsworth 说。 “所以你可以建造一个漂亮的大型航空结构,如果应用程序需要连接到飞机的另一部分,或者你正在建造的任何东西,你可以焊接那个部分。这是二合一,世界上没有多少机器可以做到这一点。”
为了质量和控制,EBAM 300 使用西亚基的层间实时成像和传感系统,可以感知和具有精确性和可重复性的数字化自调整金属沉积。根据该公司准备好的评论,这种闭环控制是西亚基的 EBAM 3D 打印工艺从第一部分到最后一个部分提供一致的零件几何形状、机械性能、微观结构和金属化学的主要原因。
Hollingsworth 指出了 3D 打印钛部件必须为 TAI 这样的客户提供的优势。 “对于像航空这样的行业处理这些非常昂贵的材料的空间,购买一大块钛或钢坯需要很长时间,”霍林斯沃思说。 “很多时候,有人可能会订购一块钛坯,它可能来自俄罗斯,可能需要 15 个月才能收到。对于我们的系统,有大量可用的电线。就切割而言,您不会浪费所有材料。当你[使用减法工艺]制造零件时,你已经浪费了 80% 的钛,而且这是非常昂贵的材料。因此,我们在这里加快了上市时间并减少了浪费。”
Hollingsworth 说打印后零件会进行一些加工,但将其描述为“最少”。他指出,航空航天业的其他大型制造商,包括空中客车公司和洛克希德马丁公司,也拥有西亚基的 EBAM 技术。 “我们很幸运,我们的很多流程都是en 批准用于陆地、海洋、空中和太空,我们正在努力实现商用飞机的采用,”霍林斯沃思说。 “当然,每一家主要的航空公司制造商都在关注增材制造并进行投资,因为他们看到了不祥之兆。”
减少生产步骤

与此同时,位于以色列洛德的 Massivit 3D 对其紫外线固化材料的化学成分进行了调整,使其具有防水性,可用于新的 3D 打印工艺。设计的为了与公司的 Massivit 10000 模型(也是新的)一起使用,稍微改变的材料 Dimengel 50 用于打印各向同性复合材料模具的外壳。
“如果您曾经见过有人为地基铺设表格,这在某种程度上是相同的概念,”北美复合材料销售经理 Mike Clark 说。 “外墙和内墙。”
在此过程中,以 1 毫米为增量打印 8 到 10 层“墙”。然后第二个打印头移入并在壁之间的空隙中分配两部分工具环氧树脂。重复打印和浇注步骤,直到模具完成。
“所以你打印一些,然后浇注一些,”Clark 说。
开放时间或混合材料的时间达到生强度大约需要 20 分钟。 Clark 说,这个开放时间允许浇注层混合,创建一个真正的各向同性 3D 打印模具。打印后和可选的二次热处理,零件浸泡在水中,这使得 Dimengel 50 壁破裂。干燥后,可以对部件进行打磨、抛光和抛光。

“模具制造商通常需要 19 到 25 个步骤来制作复合材料模具,但这可以减少到四个步骤,”Clark 说。改进流程还可以节省时间,最多可减少 80% 的时间Clark 说,劳动力减少了 90%,工具拥有的总成本最多减少了 75%。
材料、方向和速度方面的进步
In除了节省时间之外,Clark 还注意到在 10000 上制作的模具的各向同性特性。“我们的是一种固体材料,”他说。 “在 X、Y 和 Z 轴上,热膨胀系数、热变形温度——所有这些特性都是相同的,无论方向如何。在传统的 FDM 打印机中,您必须以某种方式定位部件,这样 Z 轴就不会承受负载的冲击,因为打印部件中最薄弱的环节是层压、[层的] 粘合或缺少层压。”
Massivit 与 ACS Hybrid Inc. 和 3D Composites 合作,在 Massivit 1800 Pro 上打印航空零件工具,该工具可在热成型机中承受 45 次拉力。传统上,这些工具由高密度泡沫或铝制成。 “高密度泡沫不会持续 50 次拉动,”克拉克说。金属工具会更耐用,但在热成型中,您需要模具保留一些热量,而铝是导体。
“如果您使用 CIM [铸入-运动] 155 你会得到数千 [拉动],”克拉克说。因为 CIM 155 是绝缘体,所以它在温度下的停留时间比铝长。 1800 Pro 和其他两款型号 1800 和 5000 使用该公司独创的凝胶分配 3D 打印技术,使用丙烯酸基材料。

2019 年,Massivit 与汽车零部件和宽体套件制造商 Streetfighter LA 合作开发了 2020 Toyota Supra MK5 宽体套件,i包括在 1800 Pro 上 3D 打印的 16 个部件。这些零件包括车身面板、前唇和动态尾翼。 3D 打印机的大打印量使前唇和后扰流板等部件能够在长达 5 英尺(1.52 米)的单个部件中打印。
这使得能够在 64 小时内制作原型,这比纸板、粘土或泡沫等任何传统汽车原型制作方法都要快得多。 Massivit 3D 打印解决方案上的两个打印头的可用性允许并行生产两个原型部件。可以快速创建多个迭代,从而缩短准确、对称部件的上市时间。