将不同的制造系统编织成一个有凝聚力的数字主线

在工业 4.0 之前,CAM 软件不与 ERP 系统对话或 CNC 机床静音都没有关系。信息孤岛在当时是可以接受的。当发现一家商店的不同软件系统之间存在差异时——零件编号重复、信息缺失和数据不准确等等——他们通常会耸耸肩,也许是更正,而注意到它的人又会回到任何它
这种放任自流的态度在一定程度上是由于无法在商店的许多人之间共享信息系统。那,除非有任何缺失或错误的数据直接影响您的工作职责,否则很容易说“那是他们的问题”。也没有人对机加工车间的车床和加工中心必须说的一切特别感兴趣(平心而论,在当时并不多)只要它们保持运转即可。
一切都变了
Sharing Data is Caring
MTConnect 已成为机床通信事实上的标准,而工业物联网 (IIoT) 有望制造从卡尺到厨房搅拌机“聪明”。与此同时,软件开发人员竭尽全力使他们的产品具有互操作性,以至于客户已经开始期待某种程度的数据共享,即使不是完全的双向集成。工业 4.0 似乎已成为制造业领域公认的一部分。
或者已经成为现实?大数据抛开智能设备不谈,您很有可能会制造优质零件并按时发货,就像您自公司成立以来所做的那样。 “我们进展顺利,谢谢你,”你可能会说。那么,为什么要为软件集成、强大的 IT 基础设施和云而烦恼呢?
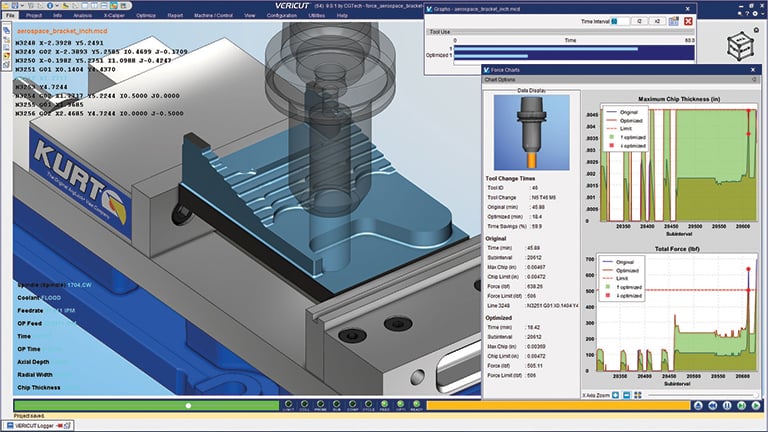
答案很简单。拥抱工业 4.0 意味着更高的制造效率。这意味着预测性维护和可预测的过程,以及在任何给定时间了解作业在哪里运行、何时完成以及您是否即将用完 ½" 硬质合金立铣刀的能力。但这也意味着您从您的工具开始,您需要重新考虑一些事情。
组织数据 With Metadata
Rich Taft 是康涅狄格州托兰市 Mastercam 开发商 CNC Software Inc. 的产品经理,他说他对 CAD/CAM、工具数据和可视化等方面的最新发展感到兴奋。实体模型已经取代了简单的线框表示。提供了广泛的工具库,以及检测碰撞和非生产性加工时间的能力。然而,也许最重要的进步是元数据使用的增加。它的意思是“关于数据的数据”,是一个在互联网上被大量使用的术语。在机械车间?没那么多。
“除了 CAD 模型本身,还有大量信息可用于简化编程和相关制造步骤,”他说。 “元数据可能包括刀具制造商、硬质合金等级、进给和速度建议、历史使用情况、替代刀具等。挑战一直是在哪里可以找到这些信息,一旦你有了我t,决定用它做什么。”
Taft 很快指出 Mastercam 能够将元数据存储在前面提到的工具库中,从而解决了第二个问题。至于第一个问题——在哪里可以找到元数据丰富的工具模型——他指出了 MachiningCloud 和 Kennametal 的 NOVO 等在线资源,它们都提供了有用的应用信息。它们还使构建虚拟工具组件变得容易,然后可以将这些工具组件拉入 CAM 软件,并存储在本地工具库中或保留在云中直到再次需要。
这样的互操作性变得更加容易最近得益于刀具数据的标准化,即用于切削刀具数据表示和交换的 ISO 13399 标准。

“例如,如果您的车间有多个 CAM 软件包,或者您正在使用刀具路径模拟软件,那么这些系统现在都可以使用相同的数据,”Taft 说。 “程序员不再需要在多个软件包中定义工具,大大缩短了学习曲线,同时减少了出错的机会。它还使 MachiningCloud、NOVO 和 CoroPlus [另一个在线资源] 的用户更容易使用。由于现在一切都标准化了,这些系统背后的人工智能能够更好地过滤掉当前工作不需要的东西。结果是工具的选择和组装变得更加直观。”
关闭加工循环
加利福尼亚州欧文市 CGTech 的 VERICUT 产品经理 Gene Granata 同意这一需求用于无缝数据交换,并指出其好处远远超出了编程部门。 “强大的连接性意味着能够与车间、工程组,甚至前台,”他说。 “这可能是一份报告,向机械师展示如何设置工作或工具库可以参考的图表来组装刀架和切削工具。无论如何,我们的目标是让现实世界与虚拟世界保持一致,然后使用该数字双胞胎来提高零件质量、刀具寿命和生产率。”
像本文采访的其他人一样, Granata 是 MachiningCloud 的忠实粉丝。这是因为在那里找到的 3D 模型——用于切削刀具和刀架、虎钳、转台,甚至机床——是刀具路径模拟和优化的必要组成部分,而且这些模型越容易访问和准确,就越有可能CGTech 的客户将取得更高水平的成功。 Granata 指出——就像 CNC Software 的 Taft——越来越多的元数据通过 MachiningC 可用由于多种原因,loud 及其合作伙伴网络改变了游戏规则。
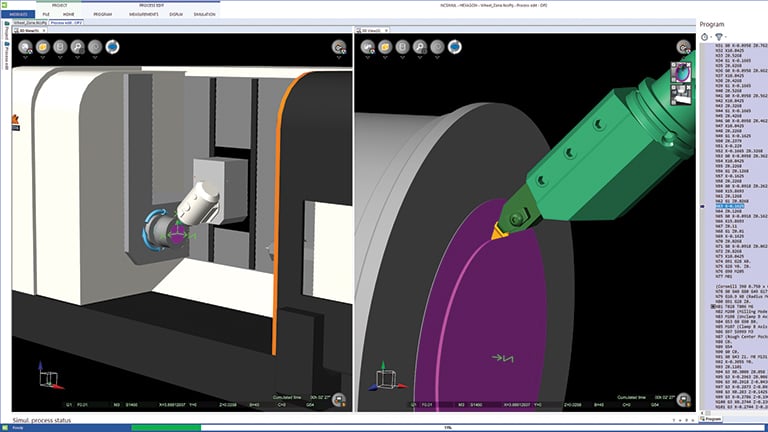
“因为你可以拉下与应用程序相关的数据以及尺寸信息,以及带有使用指南的切削刀具,它有助于简化刀具路径优化,就像我们的 Force 产品所提供的那样,”Granata 说。 “这就是为什么我们在网络研讨会和我们的用户交流中让我们的客户知道这些系统上有很多可用的智能,并建议他们将其引入他们的 CAM 系统和优化软件以开始利用它。”
存储数据的工具
Granata 和其他来源提出了另一个重要的观点:哪里最好存储所有这些信息的地方,云、CAM 还是 VERICUT?事实证明,还有第四种选择,许多离线预调仪用户已经熟悉这种选择。
“大多数商店都有多个 CAM 软件席位,有些使用多个系统,并且越来越多的商店有刀具路径模拟密歇根州安阿伯市 Zoller Inc. 的 TMS 工具管理解决方案产品线全国销售经理 Cedric Hasenfratz 说。在他们的本地系统上使用相同的刀具和刀架,而不与周围的人共享。结果是浪费精力、重复数据,而且很可能是不准确的信息。”

他说,解决方案是工具管理,例如 TMS 工具管理解决方案提供的解决方案。 Zoller 提供三个级别的 TMS 软件——铜牌、银牌和金牌——所有这些软件都提供与 Mastercam、VERICUT 和 MachiningCloud(以及其他软件)的直接接口,以及一个用于工具数据的中央数据库。
“即使是我们的入门级系统也为商店提供了一种组织所有工具和清理信息的方法,”Hasenfratz 说。 “当他们到了需要刀具寿命管理和与车间 ERP 系统集成等功能的地步时,他们总是可以升级到我们更高级别的软件包之一。重要的是他们开始行动,因为他们等待的时间越长,之后的清理任务就越大。”
构建完整的数据包
Hasenfratz 鼓励商店各种规模的人都来参加他的一个先进制造技术研讨会,他和各种合作伙伴在会上讨论如何实现“简化的端到端生产流程”。波士顿 Hexagon Manufacturing Intelligence 的 NCSIMUL 总经理 Silvere Proisy 是您可能会在那里看到的其中一位,他概述了另一种常见但不幸的机加工车间情况。
“有时发生的情况是,程序员只会定义他或她需要什么来生成刀具路径——切削刀具,”他说。 “程序然后转移到工具库或被发送到车间,由其他人决定刀架、扩展件、虎钳以及设置机器所需的任何其他东西。然而,如果车间组织良好,程序员要么从 MachiningCloud 下载这些东西,要么从他们的工具管理系统导入它们,对零件进行编程,在 NCSIMUL 中对其进行模拟,然后发送验证文件将作业和工具列表提交到婴儿床以进行离线预设。”
Christophe Rogazy 完全同意。作为位于加利福尼亚州卡马里奥的 MachiningCloud Inc. 的首席产品经理,他指出,入门只需要连接到互联网。
“拥有帐户后,您可以在 75 个(并且还在增加)中进行搜索) 工具、软件和机床合作伙伴,然后下载包含 2D 和 3D 模型的 zip 文件、XML 文件、应用程序数据(如进给和速度)以及供应商提供的任何其他内容,”他说。 “这些数据可以直接导入到大多数 CAD/CAM 和刀具路径仿真系统,以及 Zoller 和 WinTool 等 TMS 软件包中。一些系统——例如 DP Esprit——会自动从 MachiningCloud 填充应用程序参数。”
MachiningCloud 还允许用户在线组装他们的刀架,并将它们存储在私人帐户中或下载到商店的软件系统。无论如何,拥有“工具真相”的单一来源是工业 4.0 道路上必要的第一步,这将简化和简化加工操作。 “您无需成为大型商店即可使用 MachiningCloud,或拥有多个软件系统,或复杂的 IT 环境,”Rogazy 说。 “各种规模和需求的商店都将受益于它的使用。您所要做的就是登录并开始工作。”