
用于工具和砂铸模具和型芯的增材制造 (AM) 工艺得到改进,将设计和制造交货时间从数月缩短至数周。
其他优势包括减轻重量、减少潜在故障点、缩短供应链、允许生产遗留零件、减少废料、允许生产更复杂的零件以及建立更严格的质量控制。大大改进的软件、更好的硬件处理和更快的 3D 打印正在推动这些改进。
“归根结底,这就是节省时间,”总部位于马萨诸塞州伯灵顿的 Desktop M 的 Kirk Keithly 说etal Inc.,该公司于 2021 年 11 月收购了 The ExOne Co. 及其同名工业粘合剂喷射 3D 打印系统。ExOne 现在是位于宾夕法尼亚州北亨廷顿的 Desktop Metal 的子公司,为洛克希德马丁公司制造了模具。的 Sikorsky Aircraft 部门和其他部门。
“后 COVID,有很多外包业务。试图跟上进来的订单的代工厂数量激增,”Keithly 指出。 “它改变了动态。使用传统的成型技术,您需要去模型店制作模型,然后根据复杂程度等待两周到两个月来浇注您的第一个铸件。
“百分之九十九的时间,第一次铸造不好,你可能需要两到三次这样的迭代。”他继续。 “借助 3D 打印,如果他们可以打印模具和型芯,则无需传统工具即可进行铸造。
他们不是在等待模型和模具,而是在等待模型和模具。你设计你的模具,当天打印出来,然后倒下一个。它是连续生产:打印、清洁、组装和倾倒。您可以在两到三天内将完成的铸件交付给您的客户。”
在熔模铸造行业中推动采用增材制造的主要驱动力之一是能够大幅缩短制造交货时间,同时降低成本,南卡罗来纳州罗克希尔的 3D Systems Inc 的立体光刻和图 4 平台经理 Evan Kuester 补充道。
为每个零件制造注塑成型工具,”Kuester 解释道。 “通过使用 3D Systems 的 QuickCast 技术,各种航空航天客户已经看到交货时间从几个月甚至一年缩短到几天,同时在注塑模具上节省了数十万美元。”
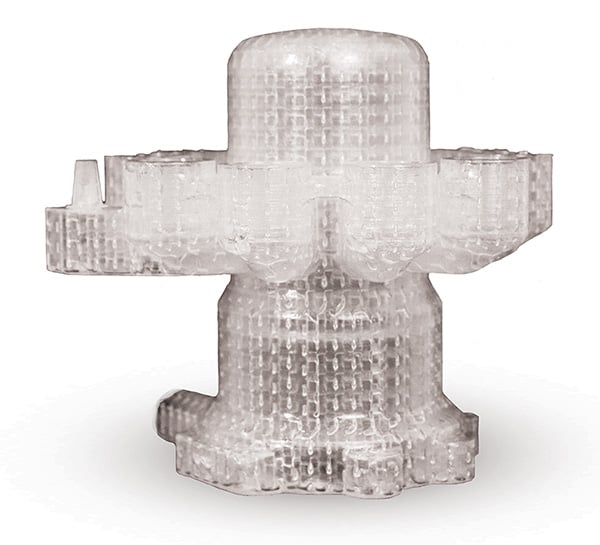
定制应用
应用包括直升机上的齿轮箱外壳、阀门和支柱。ExOne 打印机在航空航天领域的早期胜利国防是西科斯基的直升机传动装置模具。ExOne 为八个传动装置组件制造了模具,每个传动装置的设计都略有不同,Keithly 说。ExOne 设计了第一个,打印了它,交付了它,西科斯基要求进行小的改动。
没问题。
“如果客户支持 3D,那么您就可以将样板店排除在外,”Keithly 说。“设计更改很简单。它们是电子的. 你今天改变了设计。你明天就可以打印和倾倒了。”
潜在的节省可能是巨大的。
“在某些情况下,我们已经看到了 le广告时间下降了 20% 到 50%,”总部位于克利夫兰的 Lincoln Electric Holdings Inc. 添加剂解决方案业务开发经理 Mark Douglass 说,该公司专注于线弧 AM,也称为线定向能量沉积 (DED)。 “我们已经看到成本降低了 10% 到 30%,材料节省了 20% 到 30%。”
Wire DED 诞生于大约十年前,从历史悠久的焊接工艺发展而来金属堆积,道格拉斯解释道。他说,焊接金属堆积涉及将焊缝堆叠在一起以构建粗材料块来制造钢坯,然后制造零件。但该过程需要经验丰富的焊工。
借助 DED,机器人或其他自动化设备与激光或电弧焊相结合,将焊接金属沉积到熔化焊丝的熔化层中,Douglass 说。尽管添加机器人很有帮助,但软件改进才是真正的不同。
添加剂的进步
“机器人很棒;自动化很棒,”Douglass 热情地说。“但是什么在过去十年中真正实现增材制造的是软件和运行软件的硬件处理能力的改进。”
软件和硬件的这些改进也使 3D Systems 与众不同,从而大大减少了Kuester 说:“过去需要数周才能打印的零件现在可以在几小时内打印出来。”
今天的软件,带有熔化所需的过程设置库用于特定工艺的线材,可以自动采用 CAD 模型,将其切成层以在增材工艺中堆叠,然后将其发送给机器人,然后根据 Douglass 的说法,只需几分钟或几小时即可为机器人编程,而不是几天。
Lincoln Electric 开发了自己的软件 SculptPrintOS,仅专注于线弧增材制造。 “我们拥有完全的控制权,这对我们来说很重要,”道格拉斯说。 “我们可以随时进行更新。我们的焊接人员正在通知软件人员。
“如果我们的工程师遇到一个新零件,软件可能难以创建,”他继续说道,“我们与我们的软件工程师合作,可以扭转局面周围,有时在同一天。我们可以根据地面条件调整和改进软件。”
林肯电气公司为用于垂直起降的波音飞机部件打印了 3D 原型模具。该公司还使用增材制造为通用原子公司打印无人机模具。 Douglass 说:“这两个案例都经过了一系列测试并顺利通过。”
这些新兴案例的实施增材制造技术受到原始设备制造商的推动,要求供应商代工厂提高速度。与此同时,担心废料的铸造厂正在强制使用新技术——或者要求更高的价格。原始设备制造商要求在两周而不是两个月内完成铸件,而增材制造现在可以做到这一点。
对于原始设备制造商而言,缩短交货时间至关重要——甚至比节省成本更重要——并且可以决定是否赢得胜利
“这现在已经进入他们的层级,进入他们的供应链,”Keithly 说。 “它越来越被接受。原始设备制造商毫不犹豫。他们了解这些功能是什么。”
更快的打印速度发挥了作用。据 Keithly 称,ExOne 于 2018 年发布的 S-Max Pro 平台将其 3D 砂打印机的打印速度提高了 25%。 OEM 开始注意到这一点。
“如果代工厂告诉 OEM,‘我可以让第一个铸件退回k 在八周内给你,’原始设备制造商不会容忍这种情况,”基思利断言。 “他们会告诉铸造厂,‘我会去找你的竞争对手,他们可以在一周或更短的时间内把它还给我。’”
ExOne 在这方面有第一手经验。 “我们有多台机器的客户,他们只做快速车削铸件,”Keithly 说。 “他们宣传说,他们可以在五天或更短的时间内将经过机器测试的完整铸件送到客户手中。这是一个巨大的游戏规则改变者。”
与此同时,铸造厂可以将废品减少 10-60%。 “如果它是一个已经运行了一段时间的遗留类型程序,一个由 10 或 12 个零件组成的复杂核心已经存在了很多年并且存在很多装配问题,这可能会导致大量返工和报废,”Keithly说。 “如果他们正在努力解决遗留铸件问题或存在高废料问题,我们”我看到他们回到原始设备制造商那里说,‘我们不能再处理这个了。我们想在 3D 中做出改变,’”他继续说道。 “铸造厂对他们的总成本越来越敏感:我在铸造和返工上投入了多少?我什么时候说,‘停下来浇注新的铸件?’随着价格上涨,他们又回到原始设备制造商那里,但效果并不好。”
该技术的应用正在从低端发展Keithly 补充说,从中等运行原型到高速生产的原型。
事物的本质
在打印复杂的有机形状和减轻重量方面,增材制造也大放异彩. “在飞行平台的整个生命周期中,一磅(重量减轻)可节省数百万美元(节省)的额外燃料,”Keithly 说。
“ 他继续。 “当你观察大自然时,树木被设计成轻巧的 w有粗壮的枝条和粗壮的叶子。有机铸件看起来很像您在自然界中看到的。我们效仿。需要进行大量应力分析,以确保零件能够承受预期的应力或扭矩。”
改进的技术使设计更复杂、更优化的物体成为可能,这些物体的重量更轻且组件更少。 Keithly 添加。

更少的约束,简化的解决方案
“通常情况下,设计师和工程师的限制不是他们的想象力,而是用于制造对象的工具的限制,”Kuester 说。 “有时细节太小或太深以至于切割头无法触及,或者太复杂以至于无法从注塑模具中移除。在许多情况下,parts 最终的重量比预期的要重得多,因为去除多余的材料太昂贵了,”他指出。
由于 AM 零件不受传统制造的限制,设计师和工程师在
“在许多情况下,这会导致设计的整体复杂性大大简化,而任何一个单独部分的复杂性可能会变得更加复杂,”Kuester 说。 “这是因为由于使用了零件整合,这些零件现在可能在设计中扮演多个角色。
这通常会导致整体简化,比传统的方式更容易制造和安装制造的前身。”
采用增材制造设计 (DfAM) 技术可以产生巨大的影响。事实上,Kuester 说,通过正确使用 DfAM,设计师和工程师可以创造出“如此完美的形状”传统制造的零件相比之下显得笨重和陈旧。”
该技术还可以更轻松地更换旧零件,这是一个受欢迎的好处,因为制版正在成为一门失传的艺术,即使样板店可以完成这项工作,但这个过程需要几个月的时间,Keithly 说。
“我们刚刚在其中一个旧机身上帮助了一位航空航天客户,”他解释道。 “他们没有备件。幸运的是,他们有演员。如果有铸件,您可以扫描它并对其进行逆向工程。我们能够将他们的铸件发送出去,得到一个。模型,设计模具。”
虽然许多铸造厂仍处于 2D、非数字世界(主要是纸和铅笔)中,但越来越多的服务将 2D 工程图转换为 3D 图形D 模型,根据 Keithly 的说法。
在许多情况下,Kuester 补充说,AM 可以创建一个曾经有数百个单独零件的组件,并将其减少到“;一个优雅的部件,制造成本更低,而且比传统制造的部件更可靠。”
这种整合还消除了使用螺母、螺栓、垫圈和其他紧固件将所有部件固定在一起的需要,Kuester说。通过大幅减少在整个制造过程中采购、跟踪和组装数百个不同零件所花费的时间,从而减轻了重量、时间和金钱。
“零件整合的主要驱动力之一是希望减少任何给定组件内潜在故障点的数量,”Kuester 说。
例如,流形通常是通过将许多不同的零件组装成一个大型组件而创建的,有时包含数百个单独的元素。每次将零件配对在一起时,都需要在投入使用之前进行制造、组装、密封和泄漏检查。
“这些组件不仅需要大量的时间和金钱在制造单个元件时,必须在产品的整个生命周期中继续检查它们,”Kuester 解释说。 “零件合并的组件不仅更容易制造,而且由于没有接头、焊缝、垫圈和密封件,它们可能会出现故障的地方要少得多。如果没有焊缝,你就不可能开裂焊缝,”他继续说道。 “这不仅提高了复杂组件的制造速度,而且还提高了单个组件的坚固性,因为它们的故障点要少得多。”
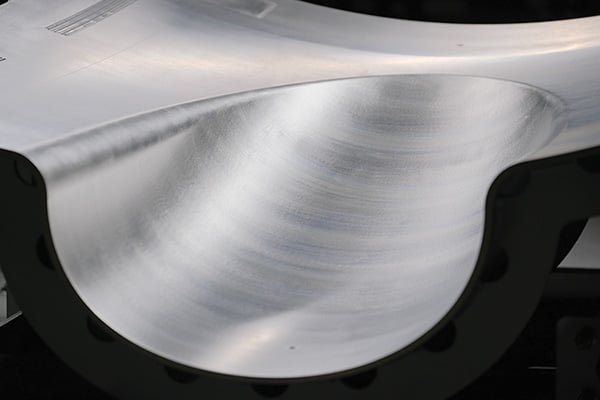
入门
增材制造的早期采用者从第一批客户的反馈中学习。
3D Systems据 Kuester 称,除了几所大学之外,它是最早在熔模铸造过程中利用增材制造模型的组织之一。该公司开始使用在其第一代机器上打印的熔模铸造实心塑料模型。
但实心模型在烧坏阶段膨胀并使陶瓷模具破裂。 Kuester 说,公司工程师最终了解到,挖空图案可以解决其中的许多问题。这导致了多年的研发,以发现镂空图案的最佳方法,这一过程促成了 QuickCast Diamond 的最新发展。
熔模铸造工艺的改进也促进了材料的进步Kuester 说:“各个行业都需要材料配方中的特定元素,以提高图案的耐用性或减少图案中的杂质。最后铸件,”Kuester 指出。 “这促使我们在过去 30 年中进行了许多材料创新,以支持熔模铸造行业。”
与此同时,ExOne 于 2002 年发布了第一台砂粘合剂喷射机 S-15,以汽车客户。 Keithly 说,反馈总体上是积极的,但客户想要更快的速度。 2014 年发布的 S-Max 的速度是其两倍。
提高速度仍然是当务之急。 “我们需要更快,”Keithly 说。 “我们需要量大。我们需要减少劳动力。”