工业自动化看起来很神奇,尤其是在装配操作中。了解您需要的基础知识,以帮助您完成下一个自动化项目。
伺服机构是 21 世纪自动化的核心。基本元件是伺服电机;一种将旋转运动转化为直线运动的装置;一套传感器提供所需的反馈;将反馈数据转换为命令信号的控制器;和启用软件。这就是高速、精密装配操作的“魔力”。随着 21 世纪基础部件的进步,伺服压力机是一项改变游戏规则的技术。

它们不仅速度快、精度高,而且还变大了。在金属成型和冲压行业,伺服压力机的产能高达 5,000 吨(4,536 公吨),更大的设备正在开发中。这些压力机正在改变用户进行工艺设计的方式,让工程师能够在整个工艺行程中实时精确控制力、速度和位置。
三十年前,行业先驱将精密滚珠丝杠组合在一起使用伺服电机、旋转编码器和称重传感器生产出第一台专门为装配操作设计的机电装配压力机 (EMAP)。
成功的早期采用者
早期采用者发现能够在装配过程中测量工艺参数,使他们能够通过将每个操作的力/位置“特征”与已知良好循环的力/位置“特征”进行比较,并实时调整压力机参数以复制产品,从而真正地“克隆”产品它。这一基本概念已用于数百种不同的装配应用,从简单的铆接到高价值电子产品的安装。以下是一些示例。
万向节组件:万向节万向节有一个中心十字或“蜘蛛”,通过将轴承杯压入臂上的孔,将其连接到一对 U 形臂上捕获“蜘蛛”上的加工日志。组装完成后,将轴承杯固定在臂上以将其固定到位。
挑战在于,在压入并固定轴承杯时,要使支架在臂中居中。这是通过一对 EMAP 实现的,这对 EMAP 在插入时同步向每个轴承杯施加相同的力。一旦杯子就位,蜘蛛就会精确居中,EMAP 同时执行放样操作。由于对支架的相对腿施加了相等的力,它保持居中,结果是一个很好的组装
此应用之所以有效,是因为 EMAP 在操作期间受到监控,并由控件实时调整力和位置。可以捕获和存储整个过程的数据以保证质量,为每个装配提供 100% 的可追溯性。该数据还可用于识别和纠正组装部件中的异常情况,从而提高整个供应链和组装过程的质量。
医用导管组装:关键操作是压接过程将小直径金属管连接到连接到导管柔性部分的较大管上。如果压接不完美,它要么在被拉上时分开,要么完全关闭管子,使导管无法使用。事实证明,始终如一地将细小的金属管压接到稍大的金属管是一项巨大的挑战。
保持质量稳定的关键在导管压接操作中,我们同时监测施加的力的大小和压接工具的准确位置。一旦捕获到已知良好操作的两个参数,力/位置“特征”将用作衡量后续操作的基准。
使用基于 EMAP 的压接站,配有外部位置传感器对导管进行压接操作。 EMAP 提供可重复的压接力,传感器监控工具以确保压接既不太浅也不太深。结果是每根生产的导管都获得了 100% 的努力测试认证,并且几乎消除了现场压接失败。

铆接球-联合装配:汽车球头内部组件是安全关键部件,通常使用铆钉连接到上下控制臂。存在三种可能的失效模式:1) 铆钉可能太长或太短,2) 铆钉可能太硬或太软,以及 3) 铆钉可能完全缺失。由于装配对安全至关重要,传统上会执行 100% 的铆接后检查。
使用基于 EMAP 的系统而不是传统的液压机,通过同时监控过程来消除 100% 的检查要求它正在执行并将“签名”与已知的良好操作进行比较。三个独立的称重传感器安装在工具中以独立测量施加到每个铆钉的力,而单位置传感器测量柱塞的行程距离。太硬或太软、太短或太长的铆钉都会在签名中产生明显的变化,孔径等超出公差的细节也会如此。
系统提供:长、短、硬、软和/或缺失铆钉检测;每个组件的 100% 认证;内置数据采集;以及每个生产零件的力和位置数据的记录——所有这些都是在过程周期中实时进行的。结果一致、准确且可追溯,这意味着不再需要对每个零件进行后处理检查以确保质量。
超越基础
它不需要早期采用者很早就意识到基于 EMAP 的系统生成的详细过程数据的用途远远超出了简单地比较“签名”和“克隆”程序集。 EMAP 供应商还忙于增强硬件和软件功能以支持更高级的应用程序。
利用这些进步的首批应用程序之一是汽车控制臂的组装,这是一种需要几何精度的产品实现适当的功能,但是由 co 制成的不能以非常小的公差经济地生产的成分。控制臂由重型冲压件或铸件制成,并带有压入到位的橡胶包裹衬套 - 显然不是极端尺寸精度的候选者。
汽车工程师通常做的是定义所需的几何形状组装并将“如何实现”部分留给供应商。供应商将此称为“幻影”尺寸,它在各种行业中都很常见。
满足“幻影”尺寸规范的传统方法是制造精确的工具和夹具,然后不断调整他们处理零件中不断发生的、不可预测的变化。其他供应商选择“压制和希望”,然后“测量和分类”并接受报废和返工成本。为了用基于 EMAP 的系统来应对这一挑战,需要先进的软件来处理额外的传感器输出集成在印刷机中的称重传感器的一侧。装配是用两个 EMAP 和两个数字探头完成的。需要这些探头是因为弹性衬套在安装过程中会弯曲,因此很难知道它们的精确位置。探头还补偿机器和称重传感器的偏转。
为了组装控制臂,将衬套压到初始位置,移除力,然后通过数字探头测量位置。一个衬套被压到与球窝接头相关的尺寸。探头测量位置并将信息反馈给控制器,控制器告诉压力机要压多远。重复此顺序,直到衬套就位。另一个套管使用相同的安装顺序,但被压到相对于第一个套管的尺寸。这是“幻影”尺寸,系统可以有效且可重复地实现它,而不管控制臂和/或衬套的变化如何。
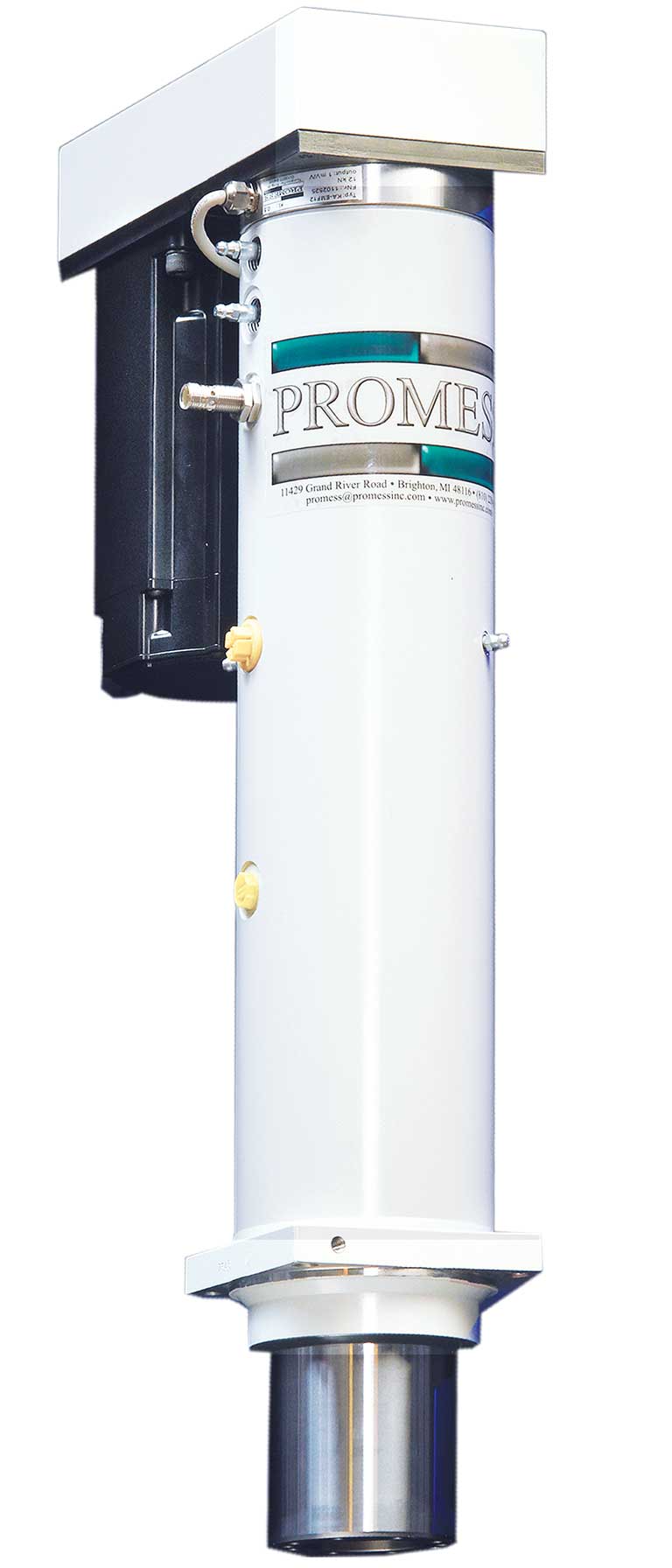
刚刚描述的系统显着提高了它组装的控制臂的功能质量,没有任何变化在组成部分的尺寸规格。事实上,很有可能放宽这些零部件的公差以降低制造成本,同时不影响成品的功能质量。功能是消费者衡量质量的标准,而控制臂系统开创的智能装配也可以成为制造商的标准。
成熟的技术
作为智能装配应用激增,因此需要启用它们的硬件和软件系统。如今,EMAP 的力输出范围从 0.2 kN 到 500 kN 和 c配备各种集成和外部传感器。它们作为单独的组件提供给系统构建商、H 型框架压力机和灵活的独立工作站供最终用户使用。
创新的工程师使 EMAP 变得足够轻,可以用作机器人末端执行器,甚至可以用作人手持有模型可用。这两种产品都适用于将压力机带到零件上的应用,这意味着压力操作的反作用力无法传递给机器人或操作员。
Promess 开发的一种解决方案用于机器人应用的是它的 Robot Press,它集成了一个集成的止动器。在操作过程中,压力机由机器人定位在零件上并接合工具。然后,机器人在两个轴上自由浮动以保持位置,同时在第三个轴上移动以适应压力机运动,直到压力机到达集成后挡块。压力机运动是完全可编程的,压力机可以配备力和位置传感器以支持智能装配操作。
线性 EMAP/旋转致动器组合
另一个趋势是线性 EMAP 与旋转致动器的组合以促进功能组装过程中的测试。例如,使用 EMAP 将汽车引擎盖闩锁与铆钉组装在一起。当铆钉被喷丸时,闩锁被启动,所需的力不断被测量,直到它达到指定的水平,此时过程停止。无论铆钉或冲压件的变化如何,该过程都会产生具有均匀驱动力的闩锁。类似的系统用于组装汽车座椅闩锁、钳子,甚至用于检查汽车差速器负载下的齿轮齿隙。
所有这些应用都依赖于复杂的控制器和软件来实时处理和集成多个数据输入时间并生成必要的伺服命令。现在可以使用具有同步功能的控件同步多个 EMAP 驱动压板机的各个角,这样每个 EMAP 都能产生保持压板平行所需的力,即使负载不均匀也是如此。
控制软件与硬件和当今的系统一起发展甚至比几年前的前辈更容易编程。供应商在系统上投入了大量时间和人才,将流程简化到通常不需要专业控制工程师的程度。
随着 EMAP 技术的成熟,智能装配和装配的概念更符合功能规范与维度相比,它在广泛的行业中变得越来越实用。然而,成熟并不意味着停滞。该技术通过提供真正创新的解决方案来应对困扰制造商数十年甚至数百年的挑战,从而不断发展。