更高的生产率促使飞机制造商部署更多的自动导引车和移动机器人解决方案以提高工厂产量
新的自动化解决方案通过自动导引车 (AGV) 和移动机器人解决方案推动航空航天生产蓬勃发展帮助航空航天和国防建设者满足交付新商用和军用飞机的苛刻生产计划。为了实现最近加强的波音 777X 计划等大型项目的生产目标,制造商越来越多地部署新的自动化来制造飞机部件和加快总装操作。
借助智能、可编程的 AGV,航空航天供应商可以减少他们对耗时的起重机移动的依赖,这些移动通常用于在整个工厂或进出工作间移动大型、重型机身和组件。此外,移动机器人更常被定位在 AGV 上,以将机器人带到工件上。航天供应许多公司正在使用更多的机器人来优化和改进喷漆/涂层应用,以及对涡轮喷气发动机中使用的压缩机叶片进行机加工、打磨、去毛刺和检查操作。

“机器人自动化有助于以一些传统和非传统方式改善航空航天制造,”Kuka Robotics(密歇根州谢尔比镇)客户经理 Dave Masinick 说). “传统的机器人自动化通常处理高产品量和快速循环时间。在航空航天中,循环时间仍然很重要,但最终产品产量要低得多。仍然很高的是每个产品所需的操作次数。
“最重要的例子是子组件的钻孔和紧固以及机身的最终组装,”Masinick 补充道。 “其他传统改进包括操作一致性以提高质量和减少返工,以及消除因重复性运动创伤造成的工人伤害。机器人正被用来取代传统机器,用于自动检测、复合材料铺层和修整/布线等应用。”
在非传统机器人自动化中,航空航天制造对移动机器人的需求不断增加,Masinick 说。 “与固定式机器人或线性轨道上的机器人不同,航空航天制造商希望将机器人移动到工作位置,而不是将工作移动到机器人旁边,”他说。 “这为他们提供了极大的灵活性产品组合并消除附着在地板上阻碍物料流过设施的‘纪念碑’。”对于移动机器人技术,Kuka 提供其全向车辆 (omniMove),通过手动操作员输入以及引导和工厂导航技术将机器人运送到工作区域。
以汽车自动化为基础
当大萧条对汽车制造商造成沉重打击时,许多供应商公司,如 Fori Automation Inc.(密歇根州谢尔比镇)转向航空航天制造业寻求新机遇。基于长期用于汽车的技术,像 Fori Automation 这样的开发人员开始设计将这些专业知识应用到航空航天领域的方法。 Fori 成立于 1984 年,目前正在验证和购买两台容量为 95,000 磅(42,750 千克)的 AGV,它们将使用工具拿起商用飞机机翼,然后将其驶入和驶出高压灭菌器,说Fori Automation 副总裁 Paul Meloche识别,销售。
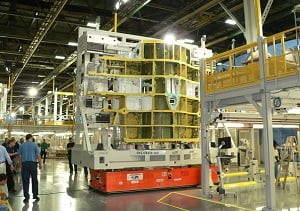
机翼 AGV 系统提供了一种高度灵活、可重新编程的替代方案,可以替代使用起重机移动非常重的大型飞机部件。 “这是我们提出的一种利基产品,它是我们多年来在整个汽车工厂中用于拾取和转移零件的汽车技术的衍生产品,尤其是汽车中称为底盘结合的过程,”说梅洛切。 “我们在全球客户群中使用了很多专利技术。”他说,这些 AGV 配备伺服驱动升降机和驱动/转向装置,可以在将前后悬架、底盘和发动机装到汽车中时准确、重复地定位 AGV,然后使用机器人手动或自动固定它。
Meloche 说,大约五年前,当公司希望将其技术从汽车领域转移时,Fori 最初将目标锁定在航空航天领域的 AGV 上。 “我们修改了我们目前为汽车制造的产品的容量和功能,并可能在四五年前将其推向市场,它才刚刚起飞。我们处于一个独特的位置,因为我们是一家技术驱动型公司,所以我们拥有许多推进和提升专利,以及用于零件 ID 和测量的视觉系统。”
Fori Automation 的第一台 AGV为航空航天交付的是洛克希德马丁公司(马里兰州贝塞斯达)用于移动中心 J470 中心机翼组件的工具夹具交付系统ly. Meloche 指出,航空航天制造商需要更有效的方法来移动工厂中的机身以实现吞吐量。 “在洛克希德马丁公司的案例中,他们有 16 个不同的单元在 F-35 的中心部分进行钻孔,那里安装了发动机,”他说。 “通常在过去,他们会将钻孔带到零件上。在这种情况下,他们将零件带到钻孔中,因此这是一个非常不同的过程。”
Fori 开发的精密磁测量设备测量磁场强度,并使车辆能够将自身定位在装配站的精度为 ±5 毫米,定位重复精度为 ±2 毫米。工具和 F-35 中央机翼部分重约 12,000 磅(5400 千克),每次将工具移动到另一个钻孔站时,AVG 都支持该公差。在每个工位,带有锁定锥细节的垂直支柱也夹在工位的底部在使用自动钻头钻孔时,提供保持孔精度所需的刚度。 AGV 进入工具下方并将其捡起,然后通过安全协议工作,然后将工具从一个工位移到另一个工位。
这种用于机器人钻孔和其他应用的自动化为航空航天制造商提供了巨大的帮助灵活性。 “我们与许多提供机器人钻孔的公司合作,因为他们需要在工厂周围移动机器人,”Meloche 说。 “整个前提是提供灵活性、模块化和增加吞吐量。减少对工厂中桥式起重机的依赖是一种驱动力,因为安全、等待起重机的低效率以及将您的零件举过其他零件顶部的安全问题。航空航天装配正在大力推动远离桥式起重机。拥有楼层引导的自动化系统可提供更高的准确性,而无需十几名操作员和观察员观看该装置在起重机上吊起,效率更高。”
Fori 为航空航天制造的大多数不同 AGV 将拾取零件——飞机驾驶舱组件、机翼、或机身部件——已经安装在固定装置上,在车辆滑到下方后由 AGV 一起抬起。 Meloche 说,AGV 具有 320-V 西门子控制架构和伺服电机,精度高且速度无级可调。 “当你在 AGV 顶部没有任何东西并且你正在沿着一个干净的通道移动时,你可能想要走得更快,但是当你有一个 60,000 磅(27,216 千克)的机翼时,它的尖端到 -尾巴 60–65' [5.6–6–m] 长,您想以非常慢的爬行速度前进。您将安装安全扫描仪以防止发生任何碰撞,并能够根据 AGV 的位置或负载量对速度进行编程。”
这些 AGV 适用于广泛的范围他补充说,许多行业,包括任何重型部件,包括风力叶片、发电机和轨道车制造,Meloche 说,他将这些机器称为 MTAV,一种多任务自动驾驶车辆。自动驾驶车辆在工厂地板上跟随磁条,使用西门子 PLC,并且可以针对不同的应用轻松重新编程。西门子手持式 HMI 悬垂手柄包括一个交互式诊断屏幕和由 Fori Automation 与西门子共同开发的 ActiveX 控制软件。 Fori 甚至开发了自己的交通控制软件,用于监控 AGV 位置、AGV 诊断和 AGV 充电状态,并与工厂制造执行系统 (MES) 软件通信,以将 AGV 引导至需要的地方。 “它的编程非常容易,100% 的控件都是在这里设计和制造的,购买后运到工厂,”Meloche 说。 “我们的目标是让工厂自行重新配置无需致电我们。”
精炼绘画过程

当被要求提高 777X 的产量时,波音公司考虑改进其商用客机机翼的机身喷漆工艺。波音公司的目标是每年制造 100 架 777X 飞机,因此转向 ABB Robotics(密歇根州奥本山)的新型机器人喷漆系统,以消除需要 35-40 名喷漆师和许多耗时的起重机移动的大部分手动流程。
波音精益推动的一部分,转向机器人自动化旨在改善机翼疼痛的流动在波音公司位于华盛顿州埃弗雷特的制造工厂开展业务。 “波音希望提高这件作品的吞吐量,”ABB 机器人高级客户主管 Timothy Brownlee 说。 “他们必须将机翼定位在垂直和水平位置,这需要起重机从一个方向移动到另一个方向。他们正在寻找减少流量的方法。机翼现在保持在单一方向,这意味着起重机移动次数减少。”
使用两个轻型 ABB IRB 5500-Aero 机器人,波音公司能够实施其 ASM,即自动喷涂方法,该方法整合了Brownlee 说,将 106 英尺(32.3 米)长的 777X 机翼喷漆到一个位置的过程在整个过程中占地面积减少了 75%,从而使吞吐量增加了 100%。手动过程需要 4.5 小时才能完成第一层涂层,现在机器人只需 24 分钟即可完成。
虽然该过程包括一些手动准备工作,包括ABB Robotics 油漆工艺经理 Didier Rouaud 指出,高度自动化的新系统 masking 会清洗、涂抹溶剂、漂洗,然后在机翼上涂上两层油漆。 “我们所做的不仅仅是喷漆,还包括在喷漆之前对机翼进行打磨和清洗。机器人在机翼上喷洒一些化学品和清洁剂,然后进行湿擦洗,”Rouaud 说。
机器人是非常轻便的六轴机器人,加上一个三轴选项,使其成为九轴轴系统,Rouaud 说,带有地板导轨系统和旋转塔架。
波音公司以前最大的瓶颈是起重机移动的等待时间。 Rouaud 说,使用新系统后,生产时间从 4 天缩短至 2.5 天,而且质量也有所提高。他说:“我们涂上了适量的油漆。”
油漆表面的外观也有了显着改善。 “当它们被手动绘制时,它们会出现Rouaud 说,“非常干燥,油漆会聚集在一起”,并指出新油漆具有湿润、非常闪亮的外观。
发动机操作所需的机器人
对于某些高精度航空航天流程,特别是喷气涡轮发动机,只有机器人才能完成工作。 “在喷气发动机生产中,尤其是在发动机叶片的前沿轮廓加工中,使用自动化系统和机器人技术是完成这项工作的最佳方式,”发那科美国公司(密歇根州罗切斯特)航空航天自动化经理 Chris Blanchette 指出. “你无法与人合作。”
他补充说,机器人自动化正在帮助航空航天制造商提高吞吐量、质量并获得更精细的过程控制。 “自动化和机器人技术真正帮助航空航天竞争满足这些要求以提高吞吐量。”
2013 年 7 月,GE 航空公司在其位于加拿大魁北克省 Bromont 的工厂开设了一个新的机器人研发中心,该工厂生产许多部件佛r GE 的飞机发动机,包括用于波音 737 和空客 320 飞机的 CFM56 发动机,以及用于波音 787 和波音 747-8 的 GEnx 发动机。
该公司投资 6140 万美元,其中 800 万美元来自魁北克政府,在 Bromont 设施位置的新全球机器人、自动化和仪表中心,这是 GE 航空公司运营的最具生产力的全球站点之一。新的研发中心正在开发先进的机器人流程、软件应用程序和知识产权,这些将出口到 GE 航空公司在世界各地的设施。
“我们正处于自动化部署的初级阶段。如果你看看我们今天制造发动机的方式,我们几乎没有抓住机会的表面,”全球自动化和仪表研发中心经理 Alain Ouellette 说。 “我们还有多个领域需要探索。如果你看汽车,他们在 1961 年安装了第一台机器人。今天,没有它们,你就找不到汽车设施。”
虽然航空航天自动化被认为是低产量,但 Ouellette 表示这种情况正在改变。 “自动化技术在过去 25 年里不断发展,复杂性已经降低,今天我们需要考虑部署更多的自动化。我们想与其他飞机发动机制造商竞争,而我们正处于某些发动机无法在没有自动化的情况下制造的地步。”
机器人视觉和检测解决方案开发商 AV&R Aerospace(AV&R;蒙特利尔) , Quebec, Canada) 是 FANUC 机器人技术的集成商,也是用于涡轮发动机叶片制造的机器人前缘和后缘仿形机的开发商。 AV&R Aerospace 首席执行官 Eric Beauregard 指出,该公司正在与 GE Aviation Bromont 工厂合作开展许多项目。
“我们专注于航空航天领域,主要是涡轮喷气发动机或能源发电,”Beauregard说。集成商开发的许多系统都用于机器人金属去除——机加工、打磨和去毛刺——以及用于复杂燃气涡轮发动机叶片的机器人视觉检测系统。 “3D 视觉检查正在开发中,”Beauregard 说,并指出 AV&R Aerospace 的客户包括所有主要的喷气发动机制造商,包括 Rolls Royce、Pratt & Whitney 和 GE。
“我们在与那里的 GE 合作,其中之一是前沿分析系统,”他补充说,Bromont GE 工厂拥有 120 多个机器人单元。 “系统用激光读取前沿,并根据获得的反馈曲线,根据 CAD 模型进行调整。它符合通用电气希望使该零件高效的公差和形状。这些部件都是锻造的压缩机叶片,然后他们需要对其进行成型,在其上成型。”
Bromont 工厂旨在增加Ouellette 指出,发动机叶片制造的生产力和机器人也有助于提高工人的安全性。通过自动化,零件的变化会大大减少。 Ouellette 补充说:“机器人可以让你在零件定位上达到小于千分之五的精度。” “如果你在手动生产中引入多个操作员,你会引入比单个操作员更多的变化。如果您可以消除这一重要的变异源,就会对质量产生巨大影响。”
本文首次发表于 2014 年 3 月版的《制造工程》杂志。