为什么要在机床上或附近使用计量设备?它不仅可用于确保工具存在或监控工具的磨损或破损情况。机内测量技术可以通过加快流程和消除额外人员来节省时间和金钱,并且它们是迈向“熄灯”制造的关键一步。监控产品制造商不断调整他们的技术以适应更复杂的加工,例如五轴或六轴 CNC 控制,以及更广泛的加工选项。

例如,低-成本机床激增。 “许多 [机床] 公司正在开发低成本加工中心,”Hexagon Metrology(北金斯敦,罗德岛)产品经理 Jean Zangao 解释说。 “例如,今天您可以找到价格在 75,000 美元范围内的 VMC。如果将其与成本为 3000 至 5000 美元(包括安装)的标准对刀装置进行比较,那是机器成本的很大一部分。”作为回应,Hexagon 品牌 m&h 推出了新的对刀仪 TS35.20。对于具有 RF 或 IR 无线通信功能的高端系统的大约三分之一的成本,它们直接针对低成本 VMC 市场。 Zangao 解释说:“对于三轴以上或比 VMC 更复杂的机器,您会需要一个无线系统。”
据该公司称,他们将 TS35.20 固定在机器的工作台上,通过电缆将其信号发送到控制单元。该公司报告偏转力下降到2.2 N•m,该公司表示允许用户以 0.5 µm 的系统精度测量直径小至 0.1 mm 的工具。测量速度最高可达 3 m/min。为了测量更小的刀具,m&h 最近推出了激光对刀仪 LTS35.65-23,专为占地面积小的机器设计。它拥有 0.2 µm 的精度,可测量最小直径为 25 µm 的零件的长度和半径。
作为对低成本端市场的另一种认可,Marposs(密歇根州奥本山)还最近推出了使用激光束三角测量的 Mida 品牌刀具破损检测器 (TBD)。
该系统将激光束投射到刀具表面,反射到接收器上。该公司表示,即使存在冷却液,其破损检测算法也将“准确分析旋转工具产生的反射光信号”。该探头适用于转速为 200–5000 rpm 的工具,直径尽可能小为 0.2 毫米。根据安装情况,工具可放置在距 TBD 装置 0.3 m 至 2.0 m 的距离处。 Marposs 的 Mida 探针产品经理 Sharad Munda 表示,该装置需要通过电线连接到机床,并且仅适用于中心切削或整体刀具。
加工变得越来越小
加工更小是计量供应商需要适应的另一个趋势。为了应对这一趋势,马波斯最近推出了用于在机刀具检查的新型高精度 Mida ML75HP 非接触式激光对刀系统。这是其现有 Mida ML75P 激光对刀仪的变体。该装置具有激光束,可检查直径小至 10 µm 的工具。 “具体来说,我们的 ML75Pico 适用于测量大于 30 µm 的工具,而标准 ML75P 适用于尺寸大于 50 µm 的工具,”Munda 说。 “我们在旧金山有一位客户测量工具的可重复性ty 为 0.2 µm,直径为 25 µm。”

ML75HP 在安装在机床工作区域内的发射器和接收器之间产生激光束。当安装在主轴上的工具中断激光束时,激光系统会向机器 CNC 输出信号。检查系统执行包括刀具长度和半径测量;刀具磨损补偿;刀具破损检测;刀片/切削刃完整性;刀片/切削刃轮廓;
为了避免激光在机床环境中出现问题,GF 阿奇夏米尔(伊利诺伊州林肯郡)提供了智能刀具测量 (ITM) 系统,供其在自己的机床上使用。在全轴速度下,相机进行高速挖掘ital 图片并处理它们。 ITM 不仅仅测量一个点;它以光学方式检查整个工具轮廓。测量的特征包括长度、直径、半径和尖端数量以及质量。通过将结果与先前存储的工具图像进行比较,它可以通过在进行测量之前以数字方式“清洁”工具图像来补偿切屑或冷却液滴等污染。该公司表示,它通常会在此过程中提供低于 ±1 µm 范围的绝对 Z 参考和刀具半径。
“有许多此类光学系统位于机器外部,”Eric Ostini 解释说,GF 阿奇夏米尔产品经理。 “机器外部的问题是系统没有考虑刀具在主轴中的位置,以及正常运行期间刀具的热量。”他还指出,工具混合在模具制造和其他制造中尤为重要。机加工操作,ITM 特别擅长测量半径和曲率的混合,确定这些关键区域的刀具磨损。
他们的加工中心本身的改进推动了对改进测量的需求。 “当我们使用线性电机驱动系统 [在我们的机床上] 时,我们发现我们的运动精度高于普通机器的能力,”他解释道。接触式探针和激光系统无法提供获得最佳光洁度、工具混合和精度所需的精度。
通过替代传感节省周期时间
还有其他确定工具磨损的方法或破损。例如,在机加工期间或之后测量零件,通常用于推断工具的状况。优点是在测量工具磨损时机器不会停止——理论上,循环时间不会受到影响,这是一个关键优势。
虽然空气量具作为测量工具不是 new,Jenoptik Industrial Metrology(Hommel-Etamic;密歇根州罗切斯特山)凭借其 TPE200 气动电子传感器将这一概念提升到了一个新的水平。该组件使用 #10 空气喷嘴将气动压力信号变化转换为数值,响应时间小于 15 毫秒。使用特定于应用的气动系统,传感器可实现优于 0.01 µm(符合 DIN 标准 2271)的可重复性,具体取决于应用。
空气计量,就其本质而言,在其范围内受到限制测量。然而,根据 Jenoptik 销售副总裁 Andreas Blind 的说法,这种精巧的设备的测量范围为 ±5 µm 至 ±500 µm,远远超出了空气测量的正常范围。包装中包含第二个传感器,用于测量供气压力以补偿变化,第三个传感器测量温度。

“当与内径的磨削或珩磨操作配合使用时,这是理想的选择,”Blind 解释说。“我们的目标是尽可能靠近机床,因此 TPE200 只有 1 平方英寸,而传统的气量计传感器则有 10 平方英寸大。”他报告说,提供珩磨或内径磨削的公司发现换能器是他们机床的有吸引力的组件。TPE200 还包含三个预定义的数字滤波器。这些滤波器可以设置为优化标准、高-的输出精度或高速测量。
另一种测量刀具磨损和在操作过程中间接破损是通过监测工具主轴上的扭矩和功率来实现的。例如,Caron Engineering(韦尔斯,缅因州)长期以来一直提供其工具监控自适应控制 (TMAC),其工作原理是随着工具切削刃的退化,切割零件所需的马力会增加。 “我们的最新产品是我们称之为 TMAC-MP 的原理的多处理版本,”Caron Engineering 总裁 Rob Caron 解释道。 “[TMAC-MP] 真正针对瑞士型机器和多功能、多用途机器,其中有多个过程同时发生。”他指出,瑞士型车床经常在无人值守的情况下运行,这使得过程控制变得至关重要。
“例如,操作员可能会在机器末端放置一个棒材进料器,该进料器可容纳 20 根棒材,每根棒材 12' [ 0.3 米] 长,而零件只有 ½” [12.7-mm] 长。在操作员需要做任何事情之前,它会运行一段时间,”他解释道。自动检测磨损或损坏的工具至关重要。 “我们的新系统允许您同时监控所有这些运动和过程。数量仅受我们选择的处理器尺寸的限制,”他说,并补充说大多数瑞士型车床同时运行的进程不超过四个。为什么要使用这种方法而不是直接感应? “激光或测头很难安装在像瑞士型车床这样狭小的空间内。这是一个非常紧张的环境。”校准曲线是通过将工具运行到操作失败来确定的,从而使这些系统更适合大批量操作。
他的公司提供的另一种间接方法是嵌入在刀架中的应变传感器——随着工具磨损,支架上的压力增加并被测量。 “我们正在测量非常小的工具,直径为 0.004–0.006” [0.10–0.15 毫米],”他解释道。他描述了分辨率低至0.001 hp,对于此类小型工具而言可能不够灵敏。
通信和 RF 的日益使用
通信技术的进步也改进了机内探测的使用。雷尼绍(伊利诺伊州霍夫曼庄园)的 Dave Bozich 表示,虽然通过电线传输的数据通常被使用红外线/光学的无线传输所取代,但射频 (RF) 具有明显的优势并且需求不断增长。 “光学需要视线 [LOS],而 RF 则不需要,”他指出。 “这使得它在机床周围更具适应性和便利性,尤其是对于大型机器,如大型 VTL 或五轴 CNC。红外/光学也受距离限制。雷尼绍可提供范围为 6 m 的 IR 系统。相比之下,我们的 RF 系统可将可靠信号传送到 15 m。”
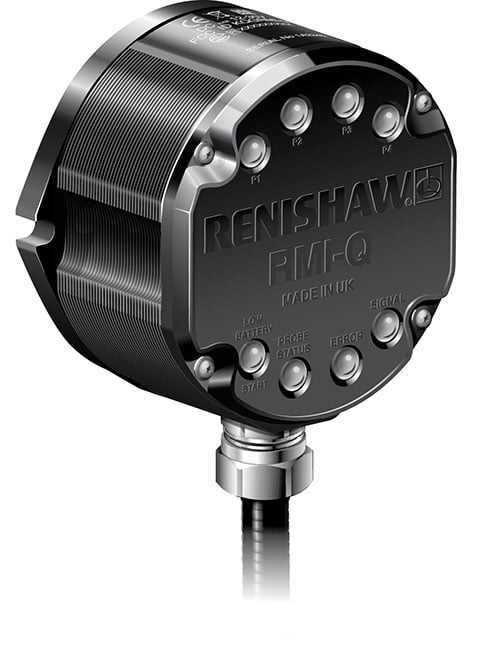
为了满足这个不断增长的市场,雷尼绍最近推出了其新的 RMI-Q 多测头无线电传输系统,用于自动启动-机床设置、刀具破损检测、零件设置和零件验证。 RMI-Q(Q 代表 Quad)在同一台数控机床上操作四个独立的无线电传输探头。 RMI-Q 是雷尼绍现有 RMI 的增强版。雷尼绍还推出了无线电对刀仪 (RTS),这是该公司专门为 CNC 加工中心或带有转台或双托盘的难以安装有线对刀仪的机器提供的射频对刀仪。据雷尼绍称,RTS 可以测量铣刀、麻花钻和立铣刀的刀具长度和直径。该公司表示,它由两节 AA 电池供电,与雷尼绍的 RMP60 和 RMP600 主轴测头兼容。
“更好的 i工具磨损的指示是根据标称值测量零件,”Bozich 说,而不是测量工具本身。这就是为什么他们开发了一系列零件探头,其中最新的是 RLP 40。它设计用于使用 RF 进行通信的车削中心。 “RF 在那些恶劣的车削中心环境中要好得多,”他解释道。 “对于 8 英寸或 10 英寸 [203 或 254 毫米] 卡盘和飞屑,您需要坚固可靠的东西。”
如果您在红外/光学或射频之间犹豫不决,海德汉 ( Schaumburg, IL) 将在 2013 年第一季度提供红外和射频混合测头、用于工件测量的 TS 460 和用于工具测量的 TT 460。用户可以选择其中一种模式:需要扩展范围和大量数据时使用无线电;需要更高准确度和快速信号传输时的 IR。 “客户要求这样做,”CNC pro 产品专家 Dan Vitullo 解释说
“尽管 IR 存在 LOS 问题,但仍有一些应用需要 IR 技术,因为它的传输速度更快,您可以更快地触发探头。您可以使用 IR 获得更准确和可重复的触发,”他说。
业内有谁在寻找这个? “我们看到了航空航天和汽车客户。航空航天对此尤为兴奋。它适用于机器上的零件足够大以阻碍探头传输到接收器单元的 LOS 的任何应用,”他回答道。 “或者在五轴加工中,您在零件中试图进行测量。”

集成和操作员
在加工中心上集成探头和传感器并轻松对其进行编程可能与创建新的一样重要。例如,马波斯推出了名为 Genior 模块化控制系统的新过程和监控解决方案来满足这一要求。 “Genior 系统背后的原理是提供一种无需人工干预即可监控流程的解决方案,”生产 Genior 系统的 Marposs Artis Systems 总经理 Jorge Pena-Mena 说。
自动化减少了培训要求也是如此。 Genior 系统专为大批量操作而设计,它提供的系统只需要极少的人机交互。 Genior 包含一个主模块,该模块与机器控制的 PROFIBUS 系统相连,用于监控机器的主轴和进给驱动器,以及一个通用测量传感器,用于与各种 ARTIS 传感器一起使用以测量力电子应变、声发射和振动以及加速度。
正如 Pena-Mena 所描述的那样,Genior 系统旨在创建一个由五到六个加工中心组成的单元,仅由一个人操作。 “它正在变成一个人类更少参与加工过程的世界,”他说。 ME
本文首次发表于 2013 年 1 月的《制造工程》杂志。