寻找提高传统减材加工工艺生产率方法的车间只需寻找减少设置时间、提高主轴正常运行时间和实施 CNC 编程效率的方法。商店经理对数字化和工业 4.0 的未来的主张不知所措,现在可以找到方法将这一令人兴奋的承诺转化为他们的日常运营。

一种方法是参观新扩建的西门子技术应用中心 (TAC) in 伊利诺伊州埃尔克格罗夫村,提供所有数字化培训——从基本加工到高级五轴培训和维护。商店可以亲自或通过互联网访问西门子的 TAC 进行培训,并了解他们的商店如何从使用西门子数字功能创建产品所采取的所有步骤的虚拟双胞胎中受益。
商店可以通过另一种方式通过考虑 GE 航空公司和波音公司在 Glass Enterprise Edition 可穿戴增强现实眼镜上使用 Upskill 的 Skylight 平台的经验,挖掘数字化的前景。使用 AR 眼镜提供了一种独特的能力,可以在车间执行极其复杂的流程(例如为波音飞机接线)或逐步组织以生产拧紧的螺栓(在 GE 喷气发动机上),这些螺栓必须完美地拧紧每个时间。
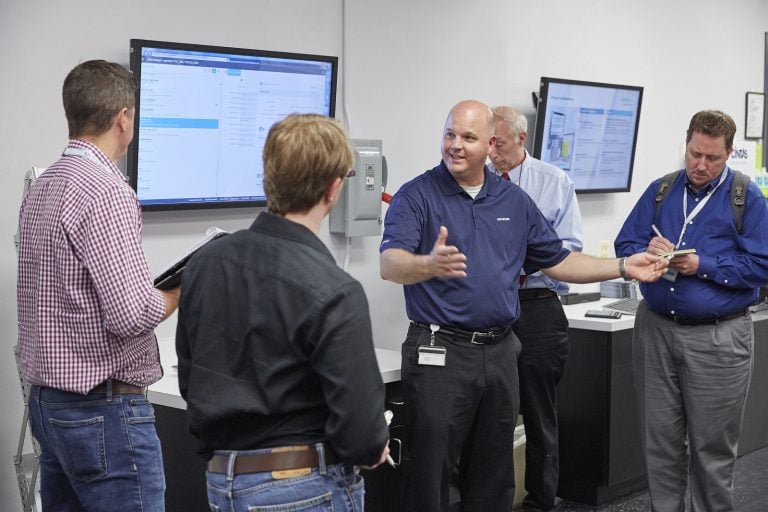
以下是大大小小的公司如何从这些和其他改变游戏规则的商店解决方案的经验和模型中受益。
西门子将其 TAC 定位于先进制造
西门子最近扩展了其 TAC 以满足培训需求,以跟上数字化和技术的快速变化。根据 Christopher Pollack 的说法,虚拟 TAC经理,“我们在扩展的 TAC 中创建了一个模拟迷你作业车间,以展示西门子的数字化能力如何将制造过程从开始一直带到物理生产。我们正在做的是采用像数字化这样的大概念和使它美味可口可在车间级别访问。”在小型作业车间中,西门子使用 NX-CAM 设计产品,对其进行工程设计并将其转化为工程图纸和文件,然后通过制造 SinuTrain 软件进行交付。
用于 Sinumerik CNC 的 SinuTrain 软件允许车间在 PC 上创建物理机床的虚拟双胞胎,并评估设置过程中通常在车间完成的所有流程。
“虚拟双胞胎允许车间做所有事情Pollack 说: “他们可以通过仿真验证流程,然后使用西门子的工业云 MindSphere 将程序传输到他们的机床。” MindSphere 是一种用于 CNC 机器、工具使用和数据传输的虚拟管理工具,它提供了验证程序和监控机器正常运行时间以及其他关键信息的能力Pollack 解释道。
明显的好处是,车间可以在虚拟环境中评估和利用流程,而不是导致机床停机,而这通常是他们在机床上进行的。 “在车间使用机床是加工车间和低生产率公司的典型做法,他们不进行基于 CAD/CAM 的繁重生产,而是进行更多需要在机器上打字的对话式编程。我们展示的是从设计产品并将其转移到作业车间的主要或一级 [供应商] 的典型过渡过程,”Pollack 说。
西门子 TAC 现在占地超过3150 英尺(293 平方米的专用空间)。机器实验室配备三台铣床(其中一台为五轴)、一个车削中心、一个 KUKA 机器人单元、一个 NX-CAM 培训站和两个升级的实践教室使用 Sinutrain 软件和 Sinumerik CNC 进行培训模拟器。 TAC 培训包括四个不同的课程;一个用于服务和维护以及三个级别的操作员培训。级别 1 侧重于基本的铣削和车削。 Level 2 引入了 G 代码,Level 3 是最先进的,专注于五轴加工。
“我们正在创建一个平行的在线培训轨道,包括网络研讨会、流媒体视频和在线讲师-领导其基础课程的培训,”波拉克说。 “我们知道,与通过在线培训可以有效处理的基础课程相比,人们参加高级五轴培训会走得更远。”
可穿戴式 AR 技术为维护提供提示
使用可穿戴增强现实智能眼镜技术和软件,可以通过一种新的方式来查看车间的事物。 GE Aviation 在其位于辛辛那提的工厂启动了 AR 解决方案。
在航空航天工业中,维护和组装错误的代价高昂,导致如果在将发动机交付给客户之前未检测到错误,则会导致生产力损失、测试和客户交付延迟以及潜在的危险结果。 GE Aviation 找到了一种新方法,通过使用可穿戴智能 AR 技术确保其发动机上的每个螺栓都完美拧紧,该技术包括来自 Upskill 的 Skylight 软件、Glass Enterprise Edition 智能眼镜和支持 Wi-Fi 的 Atlas-Copco Saltus MWR-85TA 扭矩
使用玻璃上的天窗,机械师在执行不同的维护任务时,可以直接在他们的视线范围内接收分步指导说明和图像。当机械师按照标准程序移动到需要使用扭矩扳手的步骤时,Skylight 通过智能眼镜提醒他们,然后在机械师继续前进之前实时验证正确的值。信息通过免提、声控平视显示器传递给技术人员。
可穿戴 AR 技术正在普及工人使用它来拧紧 B 型螺母,这是飞机发动机流体管路和软管中使用的关键紧固件。拧紧螺母的错误可能是太松或太紧,需要重新进行维护。当施加的扭矩尚未达到批准的标准时,Skylight 工作流程的实际视图显示红色背景。当达到 132–150 磅(60–68 千克)扭矩的最终范围时,背景变为绿色。工作人员使用语音命令或滑动 Skylight on Glass 的侧面来改变视图,并在下一个任务中前进或后退。
在部署 Skylight on Glass 之前,工作人员按照活页夹或计算机上的说明进行操作.为了满足美国联邦航空局批准的维护程序,他们经常不得不离开发动机,走到桌子或显示器前,并查看说明以检查他们的工作。使用 Skylight,可以随时访问说明以及指导视频、动画和图像。一名工作人员甚至可以打开相机和 ca所有工程师或其他支持团队成员在困难步骤中提供“所见即所得”的帮助。
AR 技术还为发动机维护文件的监管链提供跟踪结果和记录。完成每个螺母后,Skylight 会自动记录最终正确的扭矩值。为了进一步记录,Skylight 会提示机械师为每个已安装的 B 形螺母拍照,以达到历史质量目的。这些记录被上传到笔记本电脑或长期存储,作为工厂制造系统的记录。平均而言,在所有力学研究中,效率提高了 8-11%,进行测试的团队认为,一旦掌握了设备使用的学习曲线,其力学可以看到更高的效率。
可穿戴设备为波音公司提供车间的 AR 视图
波音公司的工程师已经能够使用可穿戴 AR 智能眼镜和 Skylight 软件将生产时间缩短 25% to 更快地为新飞机接线并减少错误。例如,每架新的波音 747-8 货机都有 130 英里的布线,相当于每年数千英里的布线和数万小时的工作。
布线对波音来说是一项特殊的挑战飞机,每个型号都有自己的接线方案。过去,技术人员使用充满图表的电话簿大小的参考资料。笔记本电脑有同样的基本问题:当工作人员得到指示并交叉检查图表和原理图时,不断的“视线”中断。

波音的工程师工程团队发现了一种新的可穿戴解决方案——来自 Upskill(前身为 APX Labs)的 Glass Enterprise Edition 和 Skylight 企业软件。他们开始了一项试点计划,Skylight 取代了那些笔记本电脑和纸质“电话簿”,并在取景器中显示了他们需要的说明。无需移开视线或轻敲笔记本电脑。工作人员可以通过语音命令、Glass 触摸板和头部跟踪界面在多个提示中移动。一个简单的语音命令,如“本地搜索 1-8-6-A”,可以为每根电线调出正确的分步示意图。
条形码阅读器和 Glass 摄像头有助于识别和确认电线库存.如需额外帮助,工作人员可以打开 Skylight 的“所见即所得”视频流,并与工程师或其他远程人员分享他们的观点。技术人员还可以在他们的视野中观看操作视频,从而腾出双手来完成工作。波音公司将这种改进称为可穿戴技术技术带来了“阶梯式功能变化”。布线应用的 25% 改进促使波音公司寻找可穿戴智能玻璃技术的其他应用,而不是将构建时间缩短几秒或几分钟。
需要引起注意的电动机
Volland Electric Equipment Corp.(纽约州布法罗)副总裁 Kirk Graham 表示,所有工厂,从加工车间到大型原始设备制造商,都面临着维护生产设备的重大挑战。 Volland 维修各种形状和尺寸的机电设备,包括小功率到 10,000 马力(7460 千瓦)的交流和直流电动机。
“如今,在太多情况下,生产需求胜过维护问题,”格雷厄姆说。 “虽然我们不介意进行紧急维修,但我们始终齐心协力帮助我们的客户进行预测性和预防性维护,以避免计划外停机。”
运行到故障的方法可以而且应该是一种无效,并且有许多廉价且实用的方法可以使这成为现实。 Graham 的建议如下:
“应定期检查电动机。直流电机尤其需要定期维护,可以是每天、每周、每月、每季度、每年或其他时间间隔。”他说,在确定服务间隔时需要考虑许多变量,包括应用程序/职责、环境和访问的便利性。一些应用程序比其他应用程序更重要,并且具有关闭生产或造成安全隐患的能力。 Graham 说:“在维护用于高架物料搬运的起重电机时,安全始终是最重要的。”
电机会出现什么问题?从哪里开始? Graham 指出,根据电气设备服务协会的信息,轴承故障占所有电动机故障的一半左右。甚至电气故障也更频繁机械故障的结果。未对准、润滑过度或不足、不平衡和/或潜在的结构问题都可能导致有害振动。由于绝缘老化、污染、缺乏足够的冷却空气和电压尖峰,以及其他可能的原因,确实会独立发生电气故障。
“电动机故障的根本原因故障分析是一项棘手的工作,但这是我们日常执行的最重要的任务之一,”格雷厄姆说。 “鉴于我们希望弄清遇到的各种故障的根源,因此需要与我们的客户进行详细沟通。”
无论是在内部还是在合同基础上,最终用户都必须进行测试、检查和维护他们的电机。需要对这些结果进行仔细的记录和趋势分析,以最大限度地提高收益。 “交流、直流和伺服电机通常需要对其性能以及维护和故障进行详细的测试和记录ilure 历史,以确保最大的可靠性,他说。 “我们能够及早发现机械问题,有时通过使用振动分析,但通常这可以像与操作员讨论异常噪音一样简单。
“最好的方法之一阻止电机和相关设备出现问题就是让您的员工能够自愿提供信息,”Graham 补充道。 “它可以以异常噪音、高振动、性能差或温度升高的形式报告。当从事更复杂的测试和预防性维护程序时,建议保留一本总簿或使用其他电子方式记录和趋势信息。质量员工非常关心为了防止故障而进行沟通,并且这种沟通应该以书面和/或电子方式进行。仅仅提及潜在问题通常不足以确保采取行动。”
Graham strongly 建议手头备有所有关键设备的备件。 “大型装配厂为电机、齿轮减速器、泵和许多其他对连续运行至关重要的部件保留备件。它们通常位于运行中的电机旁边,以最大限度地减少发生故障时代价高昂的停机时间。”他补充说,你并不总是需要购买新产品作为备件。市场上有大量过剩、翻新和使用过的设备,可用于经济地填补备件和零件库存中的漏洞。
车间节省额增加
商店提高生产力的另一种方法是更好地利用其设备产生的数据。流程生成的数据可以节省时间和金钱,只要这些数据能够成为当前操作的基础即可。

这是带有智能过程控制 (IPC) 软件的雷尼绍 Equator 柔性量具的承诺。IPC 软件使用最近的历史测量数据来确定过程通过全自动刀具偏移更新进行更正。据该公司称,IPC 软件提高了精密零件加工的能力,减少了设置和过程调整时间,并与自动化系统集成。新 IPC 软件的第一个版本允许连接到一个或多个机床,通过从 Equator 控制器到 Fanuc、Mazak 和 Okuma CNC 控制器的直接以太网链接。
IPC 软件允许持续监控和调整加工操作,保持部分成本nsions 接近标称并在过程控制范围内。这意味着可以快速纠正任何工艺漂移,从而提高零件质量和制造能力,同时减少废品。 Equator 量规靠近 CNC 工艺,允许在制造点进行测量和工艺调整,避免时间延迟或依赖成品(后挡板)检查。
IPC 软件对多个零件的结果进行平均,以确定调整每个刀具的真实过程意味着。出于过程控制的目的,与典型质量保证 (QA) 应用的许多特征相比,每个刀具偏置只有一个加工特征需要测量。偏移更新的频率和控制可以根据设计公差、工艺变化和工具磨损率逐个特征地配置。 Equator 测量系统可以连接到一台或多台 CNC 机床,这样来自不同机器的零件就可以在一台 Equator 上进行测量,而 offset 更新被发送到相应的机器,前提是提供了零件/机器标识。