制造和保持金属切削机床校准的科学正在改进,包括近乎实时地补偿一些误差的先进方法。

校准的必要性并不神秘。正如位于伊利诺伊州西邓迪的雷尼绍公司的校准产品业务经理 Michael Wilm 所说:“当您为汽车加油时,您需要对泵进行校准。这就是我们校准机床的原因。如果您不校准机床,您就不知道它会为您的产品制造提供可靠的服务。”
同样重要的是,当您校准你的机器,你会更多地了解它们的能力。操作员能够更好地将具有特定公差的工作分配给能够承载这些工作的机器,从而降低产生废料的几率。相反,机器制造商 SW North America Inc. 密歇根州新哈德逊市的服务协调员 Andreas Huebner 说,如果您的机器没有正确校准并且您生产的零件超出公差,这意味着机器停止生产。它将需要进行质量检查以使其恢复到运营标准。 “由于额外的劳动力和计划外的资源使用,这最终成为一个昂贵的过程,”他说。
即使校准的需求不成问题,关于何时以及如何进行校准也有很多需要了解的地方应该——以及由谁来完成。更令人兴奋的是高级误差补偿技术,它可以显着提高零件质量。
何时校准
人们普遍认为您应该校准机器在首次安装时,无论工厂校准得如何,以及此后定期校准。它可能会给你带来麻烦。它需要一个基线来与未来的检查进行比较。这些未来测试的频率,以及在某种程度上涉及的检查,取决于您制造的零件和您试图保持的公差。
Steffen Hailer,校准产品管理和应用工程主管德国阿伦的软件供应商 AfM Technology GmbH 表示,根据您的公差和机器的刚度,旋转误差(俯仰、偏航和滚动)应该每隔一到两年重新校准一次。这取决于被加工材料的硬度。 “如果机器未通过验收检查,则应在每个关键部件之前重新校准编码器,”Hailer 说。 “即使 CMM 报告中没有指出公差问题,也建议在期间每六个月进行一次校准例行维护。”
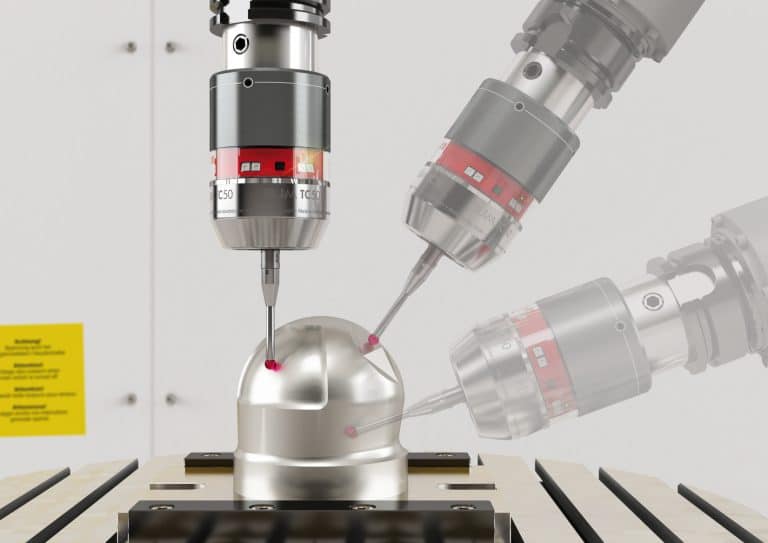
定期计划为校准带来了另一个重要好处:预测性维护。位于北卡罗来纳州夏洛特的 Okuma America Corp. 的现场服务经理 Charlie Cagle 很好地总结了这一点,他说:“你永远不会听到客户进行年度校准,因为他们所做的一切都是基于预测。如果他们发现轴中出现问题,他们会在问题很小的时候解决问题。如果你让一个小问题变成大火,你会发现自己处于零件截止日期和停机机器的枪口之下。阿尔l 如果你做了校准,你六个月前就会看到的东西。预测性维护是关于计划您的停机时间。”
您还应该在机器发生碰撞后或在更换滚珠丝杠或导轨等关键部件后重新校准机器。还有更多微妙的环境因素可能会刺激重新校准的需要。例如,该国某些地区频繁发生地震可能会产生问题。 “在西海岸和东海岸,潮汐变化导致地面波动,从而导致机器弯曲和扭曲,”雷尼绍的 Wilm 说。 “因此,在春季和秋季进行测量以查看是否有任何运动非常重要,尤其是在航空航天龙门架等轴行程为 30 米或更多的东西上。”
具有三个设备的机器-point 基地不太容易受到这种影响,但它们并不常见。即使温度恒定,如果他的位置来源随季节变化,这会改变机器的几何形状。
但“一切都与过程有关,”Wilm 说。 “你应该只定期校准一台机器,这会让你知道它何时会发生变化,而且对于每个应用程序甚至可能每个部分来说都是不同的。”换句话说,在您对您的过程了解更多之前,您不知道应该多久校准一次。
谁应该校准机器?
但只有经过培训的人员才能校准机床一些最复杂的校准工具易于使用,但在某些情况下成本很高。 Okuma 建议其机器的校准由 Okuma 经销商或经培训的车间人员完成。所有 Okuma 经销商均提供全方位服务,包括校准技术。 Huebner 说 SW 也有同感,公司将校准作为其 SW 学院维护培训的一部分。
AfM 的 Hailer 说如果他们的员工可以校准他们自己的机器,那么商店可以更加灵活并在紧急情况下更快地做出反应,这让我们回到 Wilm 关于“过程”的观点。
“拥有机器的人应该控制他们自己的过程,确保从头到尾你都在推出一个好的产品,”他说。如果您可以信任外部资源来校准您的机器,那就这样吧。
Wilm 进一步警告说,许多人不了解校准本身需要专注于机器的计划工作。 “因此,例如,如果您正在制造铝制零件,您希望在零件上移动,就像机器在铝上一样。尽管机器中的驱动机构或定位装置可能由钢制成,但您需要调整校准装置以匹配铝的热膨胀系数。”如果您不确定他是否接受,即使是 OEM 技术人员也会“弄错”
雷尼绍公司营销经理 Jeff Seliga 说,成本是一个考虑因素。可能不是,在这种情况下,您可能希望与外部服务提供商签订合同。相反,航空航天车间可能有非常严格的公差,并且作为其整体业务模型的一部分,现场需要高级校准设备以实现即时可追溯性。”
Ball Bar 提供大量信息
也许当今最流行和最有效的校准装置是球杆仪。球杆仪相对便宜且易于使用,可提供丰富的信息。只需将一个磁性安装座连接到机器主轴,将另一个安装到工作台上,然后将球杆放在两个安装座之间。球杆是一种两端带有精密球的伸缩杆。软件通过循环驱动机器路径和杆中的传感器测量与理想路径的任何偏差。然后,该软件会解释这些偏差以识别许多不同的误差源:垂直度、直线度、线性定位、齿隙、横向间隙和反转尖峰。雷尼绍 QC20-W 等系统将显示此信息在按轴量化误差时以图形方式表示几何误差和动态误差。无论机器是否移动,几何误差都会影响零件的几何形状。 Wilm 解释说,只有当机器处于运动状态时才会出现动态误差,例如轴反转时延迟引起的反转尖峰。他补充说,这样的错误会在切割型腔或圆角时在零件上产生平点。
“您可以更改球杆的尺寸以夸大您正在寻找的东西,”他说. “如果机器的一项重要功能是制作口袋,请使用非常小的球杆和非常快速的测试。如果你’在寻找几何时,您想使用非常大的球杆或非常慢的测试。这使得球杆仪可以夸大几何形状。”
另一方面,球杆仪会发现错误的组合,但不一定能准确指出错误所在。正如 Okuma America 的 Cagle 所解释的那样:“如果您的测试发现圆度错误并表明 80% 的问题是 X 轴上的反冲,您仍然需要进行额外的检测工作以确定 X 轴中的什么导致反冲。测试没有指明‘你的滚珠丝杠坏了’。”Cagle 将球杆杆称为“30,000 英尺的视图,可以看到你的机器正在发生什么,比如去看医生和做血液检查。如果你每年都这样做,你就会开始看到模式,你可以做出预测性维护决策与被动维护决策。”

最重要的是,Meyer 解释说,您还必须考虑每个轴的“位置偏差”,每个线性轴三个,每个旋转轴五个。线性轴几乎总是设计成与其他两个线性轴完全成直角(例如,X 和 Y 以及 X 和 Z 之间的 90° 角),描述实际轴和理想轴之间差异的角度总结为三方误差。旋转轴更难解释,但每个轴都有五个这样的偏差。将其添加到具有三个线性轴和两个旋转轴的五轴机器中,您有 43 种可能的偏差。 (线性轴为 3 x 6 + 3,旋转轴为 2 x 6 + 2 x 5。)
Meyer 还解释说,旋转轴中 80% 的误差通常来自位置偏差和20% 来自组件偏差,而对于线性轴则相反。
识别和测量其中一些偏差最好使用激光干涉仪来完成仪表。一些激光系统,如 SIOS SP15000 C5 和 Renishaw XM-60,甚至可以在沿轴向下移动时同时测量所有 6DOF。 (严格来说,SIOS C5 使用激光测量 5DOF,同时使用电子水准仪测量滚动。)
这些系统的精度可追溯到国际标准,并且尽您所能,因为雷尼绍的Wilm 解释说,您是在用光的波长进行测量,这是所有长度测量所基于的单位。这些单位甚至考虑了气温、气压和湿度对光的影响。例如,Wilm 说 1°C 的变化可能会导致测量中出现 1 ppm 的未补偿误差。如果不进行补偿,所有环境因素加在一起可能会在测量中产生 20-50 ppm 的误差。
但与忽略或误解材料温度相比,这些都微不足道。 “如果我使用 10 ppm 的热膨胀系数,我会每米有 1 微米的不确定性,仅 0.1°C 的不确定性会导致 1 ppm 的误差。”
因此,如果在加工铝时温度测量值偏离 1°C(膨胀系数为 24 ppm) ),误差将为 24 µm/m,这在某些应用中变得很重要。 Meyer 说,除了提供补偿标称位置的关键信息外,不断测量温度和可视化梯度“还提供了大量关于机器结构、热行为和校准过程质量的信息。但要轻松做到这一点,您需要像 SIOS 的 LCS 系统这样的无线传感器。”
其他校准技术包括 3D 探头(现在是高精度机床的标准配置)、主轴分析仪(主轴通常制造得非常高公差,然后假设在安装时是好的)和旋转轴校准器。最后一项存在一些争议,因为 m任何人都认为如果你在旋转轴上有一个刻度,你就不需要校准。但 Wilm 说这是错误的,因为大多数只有一个读头,“如果支撑环或读头的轴有任何偏心运动,你就会得到基于该偏心运动的定位误差。”
雷尼绍 XM-60 激光干涉仪在沿轴向下移动时同时测量所有六个自由度。 (由 Renishaw 提供)旋转轴校准器使用激光确定实际旋转位置。最后,不应孤立地使用到目前为止讨论的工具。将它们结合起来创建一个整体图和一个完整的校正计划。
过程中校准
如果您发现机器的某些方面不符合规格,您要么o 机械地修理它或忍受生产坏零件并冒着更大的失败的风险。但是小错误可以自动补偿,并且有解决这个问题的新技术。
旋转补偿是一个简单但重要的例子。正如 Cagle 解释的那样,在像 Okuma MULTUS 这样的多功能车床上,操作员需要找到铰接头的旋转中心来控制刀尖。否则,精确的联动五轴加工是不可能的。这同样适用于任何旋转头或铰接头,或加工中心的耳轴工作台。 Okuma 使用测试条和指标执行此检查。然后,软件使用结果自动校正头部相对于刀尖的 X 和 Y 位置。
Okuma 还提供五轴自动调整系统,该系统使用接触式探针和基准球来在大约 10 分钟内测量并自动补偿 11 种类型的几何误差,或在 30 分钟内完成更全面的调整。佛例如,Cagle 解释说,如果 X 轴和 Y 轴是直的,但探头检测到 Z 方向有轻微误差,则控制器可以“在 Z 方向插入一条直线,也许是通过在一米的过程中移动 X 两微米。”
再如,多面加工,每个面倾斜不同角度的刀具,系统自动将最大加工面误差从25μm改善到10μm。 Meyer 补充说,Siemens、Heidenhain 和 Fidia 还提供使用球体来补偿旋转轴偏差的软件选项。
位于新泽西州富兰克林湖的 Mitsui Seiki USA Inc. 不仅致力于研究更多自动误差补偿。该公司正在关闭制造循环以完成精确到几微米以内的零件,然后在它仍在机器中时对其进行验证。客户工程师 Béat Ries 解释说,该公司通过结合 SIOS 的先进激光干涉仪、AfM 的软件和 NIST tr可加工工件——由美国国家标准与技术研究院认可的实验室测量的具有多个尺寸的阶梯量规。
激光干涉测量过程完成后,校准技术人员上传间距补偿值错误、双向错误和 3D“数据量”直接发送到 FANUC 控制,无需任何额外输入。 AfM 还为 Siemens、Heidenhain、Fagor 和 Bosch 控件创建了接口。然后,控制器能够自动改进已经精确的机器。举个例子,测量三井精机 Vertex 750 机器上的 Y 轴发现在整个 800 毫米跨度内的最大定位误差为 13.4 微米,SIOS 干涉仪和 AfM 软件在一个周期内将其减少到 0.54 微米,改进了96%。
校准所有三个线性轴耗时 77 分钟,整体精度提高了 95.7%。迈耶指着 o但这些结果表明 SIOS 干涉仪对温度和气压等环境影响以及死路径误差的补偿效果如何。 “达到这些水平还需要加快校准过程,而 SIOS 干涉仪的一个优势是其高数据采集率,”他说。
此外,AfM 现在提供的软件能够确认和只需探测 NIST 可追溯工件,即可在 15 分钟内根据国际标准证明机器的线性和体积精度。更好的是,Ries 指出,如果一台机器可重复返回工件的正确测量值,那么机器对其已完成的棱柱形零件的测量值的准确性就可以信赖。这关闭了制造/QC 循环,至少在 Mitsui Seiki 机器上,使超精密加工几乎自动化。