多任务机器不仅可以提高生产力,还可以提高质量

多任务加工的吸引力不难理解。多任务机器克服了传统机器的一些局限性,并在减法加工零件方面发挥了自己特殊的魔力。从最早的车铣复合机床到当今最先进的同步加工多功能机床,制造商已经认识到提高生产率的多任务机床ing 和质量齐头并进。能够在一台机器的一次夹持中完全放下零件的能力消除了在第二台机器上进行的精度抢劫重新夹持,并提供了快速转换以满足短期生产需求的灵活性。创新的机器配置和灵活的工件夹持正在扩大未来多任务机器的极限。
测试极限并突破多任务的边界
“多任务机器开发的主要目标之一是尽量减少任何权衡,”Okuma America Corp.(北卡罗来纳州夏洛特)的车床产品专家 David Fischer 说。 “客户不想放弃他们的多任务车床的任何铣削功能,他们也不想放弃多任务加工中心的任何车削功能。” Okuma 的 Multus 系列多任务车床配备了性能与其大型加工中心相当的铣削主轴。主轴范围从 6000 至 12,000 rpm 甚至 20,000 rpm,并实现与典型加工中心相当的金属去除率。此外,Okuma 的车削功能等过去仅适用于加工中心的技术现在正在迁移到 Multus。
“有几个关键功能使多任务机床对制造商具有吸引力,”费舍尔说。 “传统上生产零件需要操作员或机器人将零件从一台机器移动到另一台机器。在每种情况下,错误加载都可能导致报废或返工。使用多任务机器,必须装载原材料并卸载成品部件。其他一切都由机器处理,消除了可能发生错误的中间步骤。在几分钟内从一项工作转换到另一项工作的能力使得响应快速变化的生产需求相对轻松。例如,该热门作业的中断不再导致多个 machine 设置来实现它。只需更换卡爪,选择程序并运行零件。”
能够实现这种快速转换的灵活工件夹持系统至关重要,Fischer 表示:“客户需要能够快速转换,在两者之间移动尺寸和形状明显不同的零件。过去,这些系统很笨重,悬垂很大,导致工作范围受限和刚性损失。最新的系统比旧系统有了很大的改进,更紧凑、更坚固。例如,我们的陈列室中有一个单元使用 Multus B300 多任务机器,该机器由 FANUC 机器人照料,它可以装卸零件,也可以将不同的托盘装卸到卡盘的表面上。这允许电池在大约一分钟内完全自动转换。使用这种类型的系统,客户可以在没有任何操作员干预的情况下从一个部件移动到另一个部件。机器人上的视觉系统不是简化多任务机器自动化的技术。借助视觉系统,机器人无需专门且昂贵的进料输送机即可找到零件。可以使用低成本的平面输送机,操作员可以将零件随机放置在输送机上,机器人将定位并在需要时定向到零件,”Fischer 说。
生产力中心具有集成托盘传输功能, ATC
“ICON flexible 系列铣车床的理念是提供具有成本竞争力的精密加工解决方案,与传统的专用旋转拨号机相比,更容易在小批量产品上进行转换”,Hydromat Inc.(圣路易斯)ICON 技术部销售副总裁 Rodger Boswell 说。提供三种版本,ICON 6-150 和 8-150 适用于 6 英寸(150 毫米或更小)立方体的工件,ICON 6-250 适用于 10 英寸(250 毫米或更小)立方体的工件,ICON 车铣机器功能 m配备四轴加工模块的加工站,配备 10,000 至 60,000 rpm 的盒式电机主轴。每个加工模块都配备了自己的 12 位换刀器,在配备齐全的 6-250/8 工位模型上总共可能有 96 把刀具可用。

ICON 6-150 和 8-150 车铣复合加工的目标工件是通常在单轴瑞士机床、VMC 和 HMC 上生产的零件。 ICON 6-250 专为大型工件而设计,例如汽车歧管和 ABS 零件。较小和较大的车铣车削之间的一个显着区别是ICON 6-250 机器的顶部可以安装总共四个三轴模块,这样就可以有两个主轴同时在工件的四个位置同时切割。
每个 6-150 或6-250 机器在第 2、3、5 和 6 站安装了四个 CNC 转台,位置精度为 ±4 秒。每张工作台都配备了 EROWA 零点夹紧系统,可将底座托盘安全准确地夹在工作台上,托盘位置重复精度小于 0.002 毫米。使用螺栓固定在模块化托盘系统上的标准或定制工件夹具将工件固定在托盘上。 “一旦工件被固定在机器外部或内部的 1 号工位(装载工位)的托盘上,它们就会被转移到其他五个工位进行切割或辅助操作。通过分布在四个切割站的流程,循环时间大大减少,从而在多个工位上以更小的占地面积产生更高的生产率nd-alone 加工单元,”Boswell 说。
新的多任务系列具有内置自动化功能
Methods Machine Tools Inc.(萨德伯里)的 Nakamura-Tome NTRX-300 多任务车削中心, MA) 通过内置的装载/卸载自动化系统和先进的操作员识别管理软件在一次操作中完成零件加工。 “NTRX-300 在紧凑型重型机器中提供最先进的多任务处理、自动化和软件,”全国销售经理 James Kucharski 说。 “NTRX-300 具有加工航空航天、汽车、医疗和其他复杂小批量零件所需的多功能性和灵活性。 Smart X Operation 软件使其成为加工精密零件系列的理想选择,”Kucharski 说。
NTRX-300 具有真正的对置双主轴,8 英寸(203 毫米)和 25 马力(18.65 千瓦)或10 英寸(250 毫米)和 30 马力(22.38 千瓦)。该机器还配备了一个 25 马力(18.65 千瓦)的工具主轴具有 12,000 rpm 和完整的五轴功能。 NTRX-300 可以在零件表面加工 10 英寸的正方形,由于 X 轴能力低于中心行程 5 英寸(125 毫米),Y 轴能力为 10 英寸,因此无需 C 轴旋转。 NTRX-300 结构紧凑,仅占 104 平方英尺(9.66 平方米),坚固耐用,重量为 37,480 磅(17,000 千克)。
紧凑型 NTRX-300 有两种型号:8″ 卡盘具有 2.5 英寸(63.5 毫米)棒材容量或 10 英寸夹头和 3.15 英寸(80 毫米)棒材容量。 NTRX-300 的主轴之间设计有 53.15 英寸(1350 毫米)的长距离,以消除多任务处理期间工具的任何干扰。该机床配备标准的 40 把刀具 ATC,并提供 80 把和 120 把刀具 ATC 选项。
“我们的新型 Nakamura-Tome (NT) 几乎处于多任务处理技术的前沿) Smart X 操作软件,”Kucharski 说。 “使用 Windows v. 8.1,它提供了操作级别的 ma用于查看操作员许可级别的管理功能。生产率监控功能显示机器的状态、生产率图表和产能利用率,以及提供详细负载信息的负载监控功能。” NT设置画面命令和按钮全部集成在一个画面中,确保操作简单。 NT Smart X 屏幕使操作员可以在观看 3D 界面检查的同时查看 NC 程序,或者在通过摄像机观看加工区域的同时查看 CNC 坐标。
CNC 取代多功能凸轮杆加工
Index Corp. 的 MS16 Plus 多轴数控车床具有六个数控主轴,用于车削、钻孔、铣削、攻丝、深加工-在其六个主轴位置的每个位置钻孔或开槽,用于加工多达 22 根棒材-mm 直径。六个主轴中的每一个的速度都可以单独控制,并在切削过程中针对每个主轴位置和刀具的每个切削刃进行变化。
Index Corp.(印第安纳州诺布尔斯维尔)的 MS16 Plus 多轴车床具有六个用于车削的 CNC 主轴、钻孔、铣削、攻丝、深孔钻孔或在其六个主轴位置中的每一个上开槽,加工直径达 22 毫米的棒材。由于工件通过六个位置自动分度,在每个位置接受两次或更多操作,因此实现了精密车削工件的高生产率。紧凑型 Index MS16 Plus 的设计旨在提供凸轮控制机器的速度和 CNC 技术的灵活性,而占地面积不超过凸轮控制多轴机器。此外,与凸轮控制机床相比,MS16 Plus 提供了极其简单的设置和更多功能的加工选项。
MS16 Plus 共有 27 个 NC 轴,包括五个 NC 切槽或镗削滑块、五个 NC 横向滑块、一个 NC 切断和/或背镗滑块、六个工作主轴、一个 NC 同步主轴、滚筒分度以及可能的 CNC 控制辅助设备的另外五个自由 NC 轴。它们都由 Index C200-4D CNC 控制器控制。六个主轴位置中的每一个都可以包括一个带有一个 NC 轴的高度稳定的切槽或镗孔滑块和一个带有两个 NC 轴(X 和 Z 轴)的十字滑块,它们以 V 形围绕每个工作主轴布置,允许使用多个在每个工作主轴上同时使用刀具。
六个主轴中的每一个的速度都可以单独控制。对于每个主轴位置和刀具的每个切削刃,在切削过程中主轴速度可以变化。即使在主轴滚筒分度期间也可以改变主轴的速度和定位,从而避免二次加工时间。对于后端加工,MS16 Plus 配备了一个由空心轴电机驱动的同步主轴,允许 s速度高达 10,000 rpm。它可以以 30 m/min 的速度在 Z 轴方向移动 140 mm,以便在 NC 切割滑块上使用 X 轴和 Z 轴连续更快地接合多个后端加工工具。为了尽可能缩短循环时间,同步主轴在不到 0.7 秒内加速到最高 10,000 rpm。
多轴数控车床复杂零件
Chevalier Machinery Inc. (Santa Fe Springs, CA) 在其经过行业验证的磨削主轴所在的同一部门内部制造、组装和测试其车床主轴。 CNC卧式车床和立式车削中心旨在满足各种行业应用。它们包括 8-32 英寸(203-813 毫米)卡盘斜床身数控卧式车床,带箱形或直线导轨,18-40 英寸(457-1016 毫米)摆动示教式数控平板模型,立式车床 8 –78 英寸(203–1981 毫米)卡盘,以及带副主轴和 Y 轴铣削的多轴车床。也用于能源行业ry,Chevalier 的 FBL-500 系列大孔径车床,摆动幅度为 40 英寸,中心间距可达 157 英寸(3988 毫米)。最大主轴孔可达 15 英寸(381 毫米)。
在 IMTS 上,Chevalier 将推出两款数控车床,用于加工具有竞争力价格的复杂工件。 “加工高度复杂的零件需要的不仅仅是简单的双轴加工,”Chevalier 的全国销售经理 Herbert Hou 说。 “我们能够使用 Y 轴和带电工具功能进行更多加工,从而消除机器之间的处理,从而实现更准确和一致的生产。”将在 IMTS 上推出的 Chevalier 机器之一是新设计的 FNL-220LSY 斜床身车床,具有动力刀具功能、8 英寸卡盘、24.4 英寸(620 毫米)最大回转直径和高达 12.6 英寸(320 毫米)最大车削直径和最大车削长度可达 20.1″ (511 mm)。
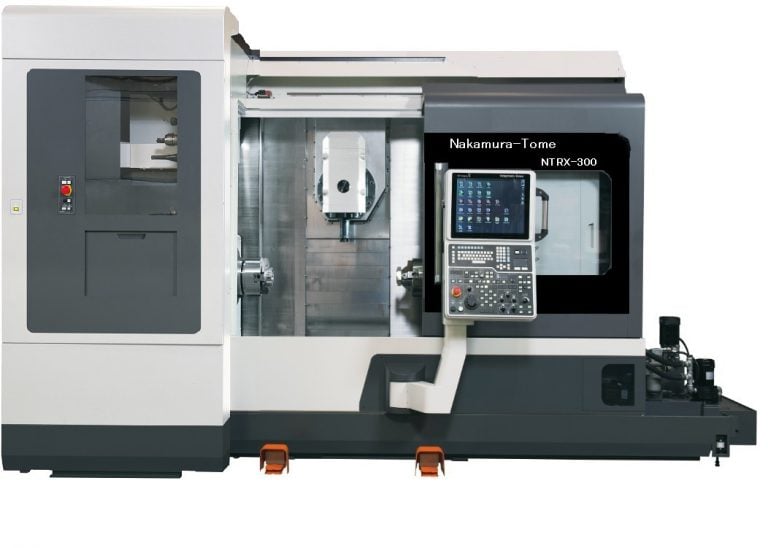
“另一个重要的自动化趋势是使用机器人装载零件,”Hou 说。“这对于大型 CNC 车床尤其重要,例如我们将在 IMTS 上推出的 FBL 360B 倾斜床身。集成的 FANUC 机器人可以处理其 15 英寸卡盘可以容纳的重型大型工件。“这些通常是大型石油工业零件,需要车削 ID 和 OD 并在法兰上钻孔。”这台机器被市场认可为FBL-360B,一款45°斜床身车床,具有刚性箱体结构和可编程尾座。它专为混合体积,短-使用 35 马力(26 千瓦)电机和可选的 50 马力(37 千瓦)主轴电机,以高达 2500 rpm 的速度运行或专用大批量应用和加工直径达 4.5 英寸(114.3 毫米)的棒材,产生高达 1901 英尺-磅(2577 牛•米)的扭矩。
副主轴车床高效完成工作
Ganesh Machinery Inc.(加利福尼亚州查茨沃斯)的多任务副主轴数控车床旨在仅在一次操作中高效地完成工作。轴向和径向铣削功能经过精确定时和去毛刺,无需为后续操作构建固定装置,也无需占用多台机器和操作员。 Ganesh 多任务 CNC 车床模型从具有 70 毫米棒材容量的八轴 Cyclone 70-3TMY 和三个 16 工位刀塔开始,共有 48 个动力刀位。使用每个工具站上的 7.5 马力(5.6 千瓦)BMT-65 工具,只需一次操作即可完成复杂的工作。该机器还提供较小的 52 毫米棒材容量,用于“一体成型”capa在 Cyclone 52-3TMY 上处理 Ø 2″ (51-mm) 棒材的能力。这两款机器也可配备带 32 个动力刀具位置的双刀具转塔。
Cyclone 78-MSY 可以使用一个动力刀具转塔加工最大 Ø 3″ 的“一体完成”工作(76-mm) 棒料或使用 10″ 三爪卡盘。这个 16 工位 BMT-65 伺服刀塔可以处理 30 多种工具。径向和轴向驱动工具可以完全访问完全同步的主轴和副主轴。 30-hp (22.3-kW) 4000-rpm 主轴和 7.5-hp (5.6-kW) 铣削主轴针对高效金属去除进行了优化。上述重型机器配备滚柱轴承直线导轨,其刚度是滚珠轴承导轨的两倍,可实现更强劲的切削,同时改善表面光洁度和极长的刀具寿命。
七轴旋风分离器CS-32 可以使用 27 把刀具加工最大 Ø 1 3/8″ (34.9-mm) 的棒材,包括 11 把动力刀具和 9 把背面加工刀具,在这个非常专业的环境中瑞士式 CNC 车床,可实现高效完整的“一体式”加工。六轴 Cyclone GTS-42 组合式 CNC 车床可以有效地处理没有或非常有限的动力刀具要求的工作,该车床配备全尺寸副主轴,适用于最大 Ø 1 5/8″(41.2 毫米)的工作).
本文首次发表于 2016 年 5 月版的《制造工程》杂志。