美国陆军正在努力研究其使用增材制造 (AM) 重新设计的符合飞行要求的发动机部件。一个这样的组件——涡轮发动机的入口涡流框架——说明了 AM 的强烈吸引力:“我们将它的零件数量从大约 150 个减少到大约 25 个,”美国制造科学和技术部门负责人 Amy Lawrence 说。陆军作战能力发展司令部、航空和导弹中心。

陆军希望入口涡流框架在五年内成为标准配置,劳伦斯说,他是最近聚集在奥本大学的五位智能制造专家之一,他们参加了一个关于任务关键部件增材制造的独家小组讨论会。
她补充说,一个更广泛的目标是 DFM(可制造性设计):获得预先更接近设计师的初衷,而无需进行代价高昂的修改。增材制造为已有数十年历史的 DFM 运动注入了新的活力。
“增材制造设计 (DFAM) 带来了一个充满可能性的全新世界,”Lawrence 说。
NASA 是“就在生产'安全关键'项目的开始阶段,”美国宇航局马歇尔太空飞行中心增材制造首席技术专家约翰维克斯在圆桌会议上说。 “对于我们的载人航天、火箭推进系统,我们没有任何符合飞行条件的安全关键部件。但我们正在制定流程和材料标准,使我们能够对这些标准进行鉴定:它是蜜蜂n 近 10 年的制作。我们可能还需要几年的时间才能真正实现这些飞行。”
NASA 已经在 NASA 硬件上为 NASA 任务飞行了“成百上千个附加部件,但这些都不是安全关键的, ”他指出。
在任务关键部件菜单上,NASA 首先选择“不承受高负载,不在最极端环境中”的更简单的部件,以证明 AM 的安全性,维克斯说。但它渴望将 3D 打印用于更复杂的零件,这些零件成本很高。
“其中一些液体火箭发动机非常昂贵,”他说,“因此我们正努力降低成本那些,也缩短了开发周期并提高了性能。”
转向高价值硬件,例如阿拉巴马州亨茨维尔的马歇尔太空飞行中心的液体火箭发动机喷射器系统专门——“将一切都以级联的方式发生,速度非常快,”维克斯预测道。

更广泛地说,NASA 正在考虑使用 3D 打印“制造可能前往火星的太空望远镜和漫游车——我们正在寻找在所有这些系统的组件上。”
2015 年 12 月,通用电气开始在其位于阿拉巴马州奥本的工厂生产 3D 打印的燃油喷嘴内饰。如今,这家已有 6 年历史的工厂拥有 46 个为 LEAP 喷气发动机制造燃料喷嘴内饰的打印机,该发动机是与赛峰飞机发动机公司合作开发的。
GE 燃料喷嘴的故事是一个分水岭AM 历史上的时刻:GE 曾经使用 20 块小金属制造相同的零件。 GE Aviation 奥本工厂负责人 Ricardo Acevedo 说:“通过增材制造,我们将其作为一个部件来制造。”
“从库存的角度来看,增材制造给我们带来了巨大的效率,因为现在你只携带一个零件,因此您的库存减少了 70-80%,”他说。 “与传统燃料喷嘴相比,它的耐用性是我们的五倍,而且与传统方法相比重量减轻了 25%,成本效益降低了 30%。”
需要采取行动
Acevedo 说,通过 AM 制造了 60,000 件后,GE Aviation 仍在“铺平道路”。 “例如,我们必须改进我们的检测系统:零件的很多复杂性都在零件内部。因此,我们必须开发与之配套的检测系统。”
如今,GE 和 NASA 发现他们正在使用 very 昂贵的体积计算机断层扫描 (CT) 扫描仪来检查 3D 打印部件。
“这确实是当今我们能够以足够彻底的方式询问部件内部以便我们进行评估和鉴定的唯一方法那些部分,”维克斯说。 “如果我们制造 1,000 个零件或 40,000 个零件,我们必须使用 CT 来查看每一个零件。”

要实现“制造系统、子系统和组件的设计,并使用合格的流程制造它们”,该行业需要在未来五年内完成Lawrence 说,多年来专注于开放标准和规范。
“对我们来说,st标准对于增材制造技术的采用至关重要,”美国宇航局的维克斯说,并指出奥本大学正在与美国宇航局、美国国防部、一些国际合作伙伴和 ASTM 国际组织(以前称为美国测试与材料协会)合作制定标准。
“在 NASA,对于这些首批安全关键部件,我们必须制定自己的标准,”他说。 “我们宁愿不从事标准制定业务。但我们不得不这样做,因为标准不存在。”
此外,制造商需要专注于“材料数据库、数字线程、文化变革、现场监控和合金开发,”劳伦斯说。
澳大利亚国家增材制造卓越中心 (NCAME) 主任 Nima Shamsaei 说,部分原因在于美国制造研究所 America Makes 和 NextFlex,制造业已经达到了一个拐点,这给这些举措带来了紧迫感burn 大学的 Samuel Ginn 工程学院。 “至少,增材制造技术的潜力已经在政府机构和行业中实现了。”
因此,他补充说,学术界必须迅速适应以提供政府和行业所需的人才。 “在过去的几年里,我们看到几乎每一所大学都试图进入这一领域。我们看到全国各地、世界各地的活动。在研讨会和研讨会方面,我们看到了来自不同行业以及大学的大量参与。” (奥本大学的 NCAME 今年从 NASA 获得了一份价值 520 万美元的研发合同,致力于研究液体火箭发动机的再生冷却推力室组件。)
仅设计工具的问题就说明了需要完成的复杂工作,Shamsaei 说. “添加剂是一个复杂的过程。考虑激光/材料相互作用、热现象、凝固、微观结构演变、缺陷形式化等等。在拥有经过验证的增材设计工具之前,我们需要积累大量知识。”

奥本工程学院南方先进汽车制造联盟主任格雷格哈里斯说,另一个必须解决的问题需要解决的是“特定发现学科的文化,每个人都在想,‘我的数据就是我需要的,我不会与任何人分享它’。”
“如果我们有一个完整的数字线程,我们已经捕获了关于母体的所有数据ial,过程,几何和测试评估,我可以实时看到它 - 在它被制造的时候 - 约翰可以实时看到它 - 在它被制造的时候 - 现在我们有那个零件看起来的可信来源就像,”他说。
“不仅如此,我还可以用那组数据识别出那个特定的部分。所以现在我知道了血统,我知道关于这种材料的一切。当它到达组装时,他们可以把它拉进来,扫描它,说,‘看,这就是那个部分。这是与之相关的所有数据。”
像这样的场景将允许预测功能以及生成设计。在创成式设计中,设计人员将零件的设计目标以及成本约束等变量输入到生成一系列可能设计的软件中。该软件可以从每个查询中学习,以便通过更多查询生成更有用的设计选项。
“我们不能那样做今天,”哈里斯说。 “我们正朝着那个方向前进。但我们在处理系统之间缺乏互操作性的过程中遇到了问题。”
与数字主线一起,开放标准,例如产品模型数据交换标准 STEP,再次非常受欢迎
“现在缺乏标准是很严重的,”Harris 说。 “标准帮助我们提高可靠性。如果我们要拥有可复制的零件,我们的材料、工艺和几何形状的可靠性是必要的。需要可复制的部件才能获得认证。
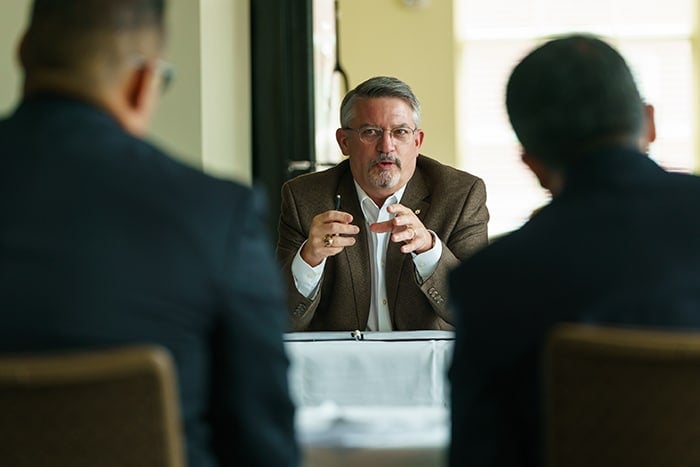
“我们正在做的事情在添加剂方面(在奥本)做的很棒:我们正在收集有关 mate 的重要数据里亚尔和过程。但我们仍然在个人、实验的基础上做这件事。在我们达到可以开始标准化的程度之前,因为我们有足够的关于流程和材料的数据,能够以一种有意义的方式进行数据分析,我们不会真正达到目的我们可以相信那些标准,John 说他需要这些标准才能使零件获得飞行资格。”
标准正在进行中
制定增材制造标准的一个挑战是,标准制定过程是基于共识和自愿的,Shamsaei 指出:“这是一项相对较新的技术,大量知识产生于不同的工业部门。我敢肯定 GE 对 AM 了解很多,但那是他们的知识产权。他们不会走进房间并分享他们所有的秘密。”
“我们分享,”Acevedo 说,并指出 GE 经常与奥本工程专业的学生合作进行高级设计项目和nd 是 Auburn 领导的 America Makes 资助的 AM 项目的一部分。但它仅限于原材料测试的数据——对于像 GE 这样“跳进增材制造”的任何公司来说,开放标准将降低基本开发成本,他补充说。
尽管如此,ASTM 正在资助支持标准的研究——其中一些在奥本。
奥本的 Shamsaei 团队计划下个月向位于奥本的 ASTM 标准委员会展示一组由 ASTM 和一些美国政府机构资助的研发成果巴黎,他说。