ComauFlex 不仅仅是一个灵活的生产系统——它是一种现代模块化制造战略
随着世界各地的汽车制造商开始投资于采用各种先进轻质材料制成的产品和部件,ComauFlex 车身在过去十年中开发和完善的车间解决方案一直在展示它如何在整合各种工艺的同时适应不同的材料。通过使用模块化、可集成和内在灵活的系统优化工作区域的布局,这种制造方法已被证明是符合时代要求的具有成本效益的解决方案。

Comau 总部位于意大利都灵,在密歇根州绍斯菲尔德设有北美办事处,拥有 40 多年的历史提供生产系统的经验,包括完整的车身车间。它认为 ComauFlex 不仅仅是一个车身修理厂解决方案,将该系统称为“先进的制造策略”。
从头开始构建以帮助原始设备制造商 (OEM)为了满足市场的动态变化和需求,ComauFlex 提供当今汽车制造商所需的解决方案:操作灵活性、最低设施要求、大批量和多种型号,以及使用先进材料连接技术的可能性。换句话说,ComauFlex 使生产工厂的传统概念现代化。
“ComauFlex 哲学是柯马过去开发和完善的装配工艺和组件演变的顶峰10 年,”柯马全球解决方案开发产品工程和管理总监 Ennio Chiatante 说。
Chiatante 说,ComauFlex 在产量、车型数量、生产物流管理和先进材料(如铝和高强度钢)的使用方面为汽车制造商提供了“极端的操作多功能性”。这意味着采用该系统的公司获得“在时间、长期成本和运营效率提高方面显着节省,”他说。
在使用 ComauFlex 系统或其组件的汽车制造商中,包括菲亚特克莱斯勒汽车公司(FCA)。在一家工厂中,ComauFlex 使菲亚特能够在同一条生产线上生产两种截然不同的车型,即菲亚特 500 和菲亚特弗里蒙特。福特汽车公司也使用该系统制造其新款福特 F-150,该车型经过重新设计,采用主要由铝制成的车身。
ComauFlex 使福特能够提高生产能力、减少在制品、改进材料物流、节约能源并最大限度地减少占地面积白车身 (BIW) 制造所需的空间。该系统还支持高速传输、高密度连接、灵活的零件处理、灵活的物流、完整的模型灵活性和最多四个独特模型的随机构建顺序制造。
着眼于未来
柯马在汽车行业已有 40 多年的历史,并且在车身装配、子组件和完整车身车间的生产系统方面拥有广泛的专业知识,柯马在提供满足市场要求的多功能交钥匙工厂。
早在原始设备制造商开始努力满足 2025 年二氧化碳排放标准之前,柯马就已经在研究能够适应的制造解决方案轻质材料组合。 “柯马始终将其发展努力集中在车身装配行业的未来市场趋势上,其中包括对最高柔性的需求Chiatante 解释道。
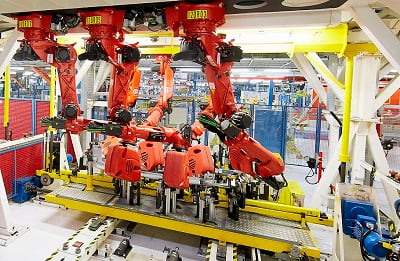
在车辆制造中使用先进材料的主要优势是减少车辆重量可以提高车辆效率,从而减少排放。例如,在 BIW 中,车辆质量减少 8-10% 可以产生约 3-4% 的明显燃油经济性节省。
随着今天的原始设备制造商开始关注每一个在混合工艺、产品和材料方面,许多公司开始将多种材料集成到同一辆车中,甚至是在同一车身结构中。这种现象是由两个主要因素驱动的。首先是优质轻质材料变得越来越普遍,这意味着它们更容易被使用可用。第二,也许是更重要的考虑因素,是它们的价格开始下降。
随着材料组合的扩展,不仅包括铝,还包括镁、碳纤维和增强塑料,创新连接过程正在改进并用于补充传统的连接过程。事实上,在过去几年中,汽车制造中部署的生产率和不同连接工艺的种类都显着增加。此外,虽然其中许多技术(例如电阻点焊、电弧螺柱焊和激光焊)是钢材常用的工艺,但在与先进材料一起使用时,它们可能有不同的应用要求。
为了支持与多材料方法相关的固有困难,并确保其客户的持续成功,Comau 的 ComauFlex 制造解决方案可以适应新材料和新连接在流线型和灵活的生产解决方案中整合流程/结构类型。换句话说,它完全满足当今的主要市场驱动因素:可扩展性、模型灵活性、对新流程的适应性和优化的物流。
在提高灵活性的同时重组 Bodyshop
与具有多个进料点的传统制造系统不同,ComauFlex 理念基本上将生产重组为两个完全相互关联的不同区域。在这个结构中,所有材料都在生产线的开始处被组装并装载到零件载体中,然后通过构建序列自动传输,机器人在每个单元中根据需要移除零件。这消除了使用叉车、货架和小零件输送机进行零件线侧供应的传统方法。随着更快的零件进给和装载、更少的传送带以及故障或零件短缺的可能性降低,汽车公司可以看到MTBF(平均无故障时间)和 MTTR(平均修复时间)的显着改进。
柯马对传统车身修理厂的重组不仅在设计上具有革命性,而且在愿景,因为它考虑了整个工厂,而不仅仅是单个流程。
这种方法的优势很明显:更好地安排工作活动,细分并集中在特定区域,减少了操作待机时间,还减少了完成整个生产过程所需步骤的数量。
模块化制造系统
ComauFlex 的基本组成部分制造方法是生产系统的主要和子装配线——VersaRoll 和 VersaPallet。由柯马开发以支持其灵活的制造理念,两者都是模块化系统,配置用于解决整个生产过程,重新定义安排和结构确保所有车身装配线。这两个系统都确保通过生产线快速传输材料,从而减少非增值时间。由于其标准化和模块化,电池可以完全组装和测试后运送到工厂,从而缩短安装和启动时间。
更具体地说,VersaRoll 是一个闭环组件,并且连接系统,主要用于设置子组件的几何形状,例如车身侧面和底盘。另一方面,VersaPallet 系统可以定义为一种高性能在线传输系统,用于完成车身底部和框架、连接和装配操作。它基于通过线路移动车身的 GeoPallet,能够取代系统中组装的各种模型所需的固定车身底部工具。

ComauFlex 方法的另一个重要部分是创新的车身加框站,称为 Comau Open RoboGate,它集成在 VersaPallet 加框生产线中。 Open RoboGate 是一个模块化、灵活且可扩展的系统,最多可配备 18 个机器人和多达 6 个专用框架门。所有三个系统——VersaRoll、VersaPallet 和 Open RoboGate——都使用倒置机器人,使生产线能够使用尽可能高的机器人密度,从而减少生产系统的整体占地面积,并在每个站内实现更高的连接操作量.
ComauFlex 的理念在其构造上也是独一无二的,因为它是一个围绕标准产品构建的模块化系统,这些标准产品结合在一个可扩展的设计框架中。这意味着可以在降低风险的情况下扩展生产环境到现有的生产和在有限的时间框架内。可以通过将称为 BRIC(基本机器人集成配置)的附加模块添加到同一条生产线并重新定位最终站来执行此扩展。而且由于每个预组装的 BRIC 电池在到达时都已准备好安装,与传统方法相比,生产线可以在更短的时间内进行扩展。
因为 ComauFlex 能够管理大量和多个紧凑型多功能工作单元内的模型,许多世界上产量最大的汽车制造商目前正在使用 ComauFlex 系统来优化装配流程、提高生产能力、减少在制品、改善材料物流、节约能源并最大限度地减少装配所需的占地面积白车身制造。
“柯马的目标是提出创新和高效的方法来为我们的客户优化生产流程,同时尊重每个客户的独特需求ements 和期望。出于这个原因,我们更愿意与我们的客户合作,共同开发能够充分满足他们的生产和投资要求的最佳解决方案,”Chiatante 说。 “事实上,考虑到它们可以独立使用,没有必要安装所有三个系统。”
例如,沃尔沃最初购买了一条完整的 VersaPallet 生产线,尽管它当时倾向于不采用顶置倒立机器人高密度站的原则。
2013年,公司TA3项目启动,沃尔沃汽车委托柯马设计、安装和调试几条新线,包括框架线、车底修复线、车顶线、激光线和空气再循环系统的部署。在包括沃尔沃及其外部合作伙伴在内的团队中合作,该生产线围绕柯马的 Open RoboGate 结构构建,这是一种模组确保高可重复性并可处理多达六种不同模型的模块化系统,以实现最大的灵活性和投资回报。紧凑精益的架构可实现高密度点焊。
同样,捷豹路虎采用了VersaRoll和VersaPallet系统生产即将上市的新车型2015 年,要求柯马将其标准框架站整合到新的柯马生产线中。
ComauFlex 的运营战略改进了生产物流管理并处理先进的连接材料,包括铝、高强度钢等.然而,它也确保了先进的操作灵活性。这是因为 ComauFlex 能够在一个紧凑而完整的多功能工作单元内管理大批量和多个模型。结果不言自明。
本文首次发表于 2015 年 9 月版的《制造工程》杂志。