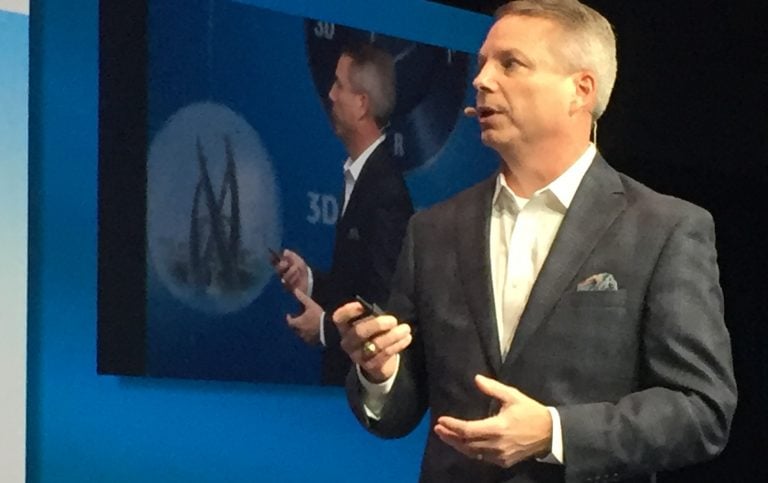
佛罗里达州好莱坞——为了缩短本田的上市时间和生产力,这家日本汽车制造商与法国软件巨头达索系统就规划结构展开合作,包括一个新的模型过程开发 (NMPD) 项目,Ron Emerson 本周在达索北美 3D 体验论坛活动上说。
本田开始使用达索产品“几十年前,当我们刚刚从 2D 转换为3D,”Hon 虚拟成熟团队副总工程师 Emerson 说。大北美。今天,本田使用 DELMIA V6。
Emerson 的“虚拟成熟团队”的愿景是,他说,“充分发挥虚拟方法的潜力来模拟‘Gemba’。Gemba 是我们的一个词在本田内部使用表示现实或实际位置。我们希望模拟、虚拟世界看起来与我们的制造情况一模一样。”他展示了加拿大一条虚拟和实际 CR-V 生产线的并排图像,称本田最近才开始“将产品置于工厂环境中,这样我们就可以验证车辆的所有新模型方面。”
本田的“全球制造模拟器”首先着眼于整体产品开发——从早期概念阶段一直到客户交付。
这家汽车制造商最近选择“真正推动达索到创新其工具”,以便在公关过程中使用“创新流程”艾默生说,产品开发比以往承担“更多的虚拟验证”。 “这尤其重要,因为本田的愿景是实现“主要是数字验证”,他指出。
本田需要在制造的产品和工厂的背景下整合产品、流程和资源。他说,要准确模拟实际现场,需要能够看到任何车辆,以及它的任何变化,具体的计划内容和具体的计划资源。
“所有本田工厂都有不同的特点”因此,这项任务具有挑战性,艾默生说。可视化“产品序列、构建、工厂的实际载体、车身位置以及在特定构建位置应该安装在汽车上的所有零件”是一项具有挑战性的任务,而本田的愿景可以以目前的能力无法实现,并挑战达索“完成更伟大的事情。”
流程规划人员很难“想象他们正在组装的东西,因为他们只是输入零件号和流程顺序,”他说。
本田为达索提供了一份长长的必备物品清单:它需要使用 3D 数据,并且需要派遣。它不需要繁重的 CATIA 数据。而且,最重要的是,它必须简单。
两人合作了两年多,“开发了一个很棒的产品:Planning Structure,”Emerson 说。
“我们可以将所有就像我们以前从遗留系统做的那样,以产品流程和资源数据为起点,在流程工程师进入并进行所有更改后,我们可以快速了解零件消耗,”他说。 “这对于确保我们不会忘记整个过程中的任何部分至关重要。”
对于车辆的每种变体来说,这都是相同的过程。在可视化中,部分尚未消耗的部分是橙色的。
“因此,[现在] 工艺工程师很容易理解他们必须应用该部分,”艾默生说。 “一旦将零件应用到序列中,我们就可以计划序列时间以及随之而来的所有要求。”
时间条目至关重要,因此工艺工程师可以“始终平衡”跨越整个生产线,或者至少在工作单元内,”他说。 “当然,最后他们可以通过再次查看正确颜色的图像来确认最终装配顺序。”
两人没有使用 CATIA 数据,而是选择了 NAV REP,“一个非常轻量级的我们可以创建数据,以使其非常直观,并且非常 [快速且] 容易转向,”艾默生说。
在“简单设计”方面,达索和本田提出了一个阻力-and-drop 过程,用于将零件分配给过程序列。
“它&rs“这非常简单:我们的工艺工程师对使用它感到非常兴奋,他们刚刚开始在开发中的一个模型上使用它,”他说。
一旦零件被分配到工艺序列,他补充说:“您可以询问流程步骤,它会突出显示该部分并说,'是的,这就是我想要放入的正确部分'。”
当需要移动东西时, “这也是拖放、剪切和粘贴,很容易将其剪切、放入,并且很容易向前移动,”Emerson 说。 “进行调整后,分配给产品的总处理时间计算也会相应调整。它非常聪明。”